Wear-resistant alloy, silicon alloy grinding ball, silicon alloy grinding section and preparation method thereof
A wear-resistant alloy and silicon alloy technology, applied in the field of wear-resistant alloys in the field of metallurgical technology, can solve the problems of low chromium content in silicon alloy grinding balls and silicon alloy grinding sections, and are not easy to break and wear, and achieve excellent impact damage resistance. capacity, improve the efficiency of the mill, and save energy
- Summary
- Abstract
- Description
- Claims
- Application Information
AI Technical Summary
Problems solved by technology
Method used
Examples
preparation example Construction
[0028] Preparation method of wear-resistant alloy material
[0029] Follow the steps below:
[0030] Step 1, batching, adding pig iron, ferrosilicon and ferromanganese to an intermediate frequency electric furnace to smelt molten iron. In this step, one or more of ferromolybdenum, ferrochrome and recarburizer can also be added;
[0031] Step 2, the molten iron is tempered, using a spectral direct reading instrument to detect the composition of the molten iron, and using a general conditioning method, so that the composition of the molten iron is, in terms of weight percentage, carbon is 3.30-4.70%, silicon is 1.0-3.50%, Manganese is 0.30-1.60%, chromium is 0.10%-1.40%, and the balance is iron and unavoidable impurities; if ferromolybdenum is added in step 1, the content of molybdenum is adjusted to 0.1-1.10%;
[0032] Step 3, out of the furnace and tempered, the temperature of the molten iron is 1500-1800°C, adding rare earth magnesium and ferrosilicon into the ladle, pourin...
Embodiment 1
[0037] Step 1, add 1020 kg of national standard GB718-82, 14# pig iron, 20 kg of ferrosilicon (content 72%), 20 kg of ferromanganese (content 65%), and 5 kg of ferromolybdenum (content 60%) into the intermediate frequency electric furnace for smelting into molten iron;
[0038] Step 2, adopt spectral direct-reading instrument to detect molten iron composition, and adopt general tempering method, make the composition of molten iron, by weight percentage, carbon is 3.30% (for the national standard pig iron comes), silicon is 3.20%, manganese is 1.50%, chromium is 0.10% (provided by the national standard pig iron), molybdenum is 0.3%, and the balance is iron and unavoidable impurities;
[0039] Step 3: When the temperature of the molten iron reaches 1550°C, it is released from the furnace. Before the furnace is released, 13 kg of rare earth magnesium and 6 kg of ferrosilicon (content 72%) are put into the ladle, and then the molten iron is poured into the ladle to incubate and bo...
Embodiment 2
[0047] Step 1, the national standard GB718-82, 1020 kg of 14# pig iron, 18 kg of ferrosilicon (content 72%), 1.5 kg of ferromanganese (content 65%), 20.6 kg of ferrochrome (content 58%), industry standard YB / T192- 6.5 kg of 2001 type recarburizer (content 98%) is added to the intermediate frequency electric furnace for smelting into molten iron;
[0048] Step 2, adopt the spectral direct-reading instrument to detect the composition of molten iron, and adopt the general tempering method, make the composition of molten iron, by weight percentage, carbon is 3.90%, silicon is 2.60%, manganese is 1.0%, and chromium is 1.3% %;
[0049] Step 3: When the temperature of the molten iron reaches 1500°C, it is released from the furnace. Before the furnace is released, 15 kg of rare earth magnesium and 7 kg of ferrosilicon according to the national standard GB 4138-1984 are put into the ladle, and then the molten iron is poured into the ladle to incubate and boil. The molten iron is cast ...
PUM
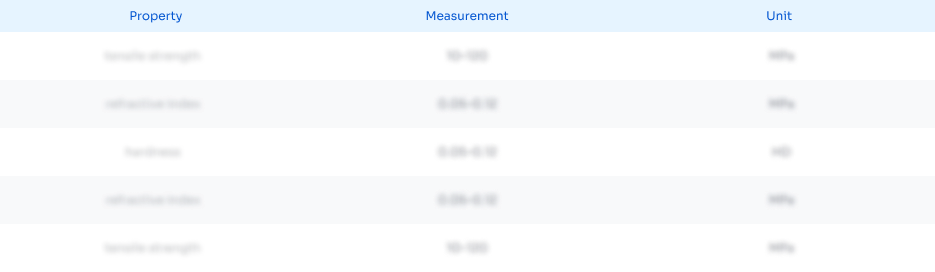
Abstract
Description
Claims
Application Information

- R&D
- Intellectual Property
- Life Sciences
- Materials
- Tech Scout
- Unparalleled Data Quality
- Higher Quality Content
- 60% Fewer Hallucinations
Browse by: Latest US Patents, China's latest patents, Technical Efficacy Thesaurus, Application Domain, Technology Topic, Popular Technical Reports.
© 2025 PatSnap. All rights reserved.Legal|Privacy policy|Modern Slavery Act Transparency Statement|Sitemap|About US| Contact US: help@patsnap.com