Preparation method of electroplating-grade copper sulfate
A copper sulfate, electroplating-grade technology, applied in copper sulfate and other directions, can solve the problems of high impurity content of copper sulfate, affecting product quality, etc., and achieve the effects of simple and easy preparation method, improved product quality, and low processing cost.
- Summary
- Abstract
- Description
- Claims
- Application Information
AI Technical Summary
Problems solved by technology
Method used
Image
Examples
Embodiment 1
[0030] The industrial-grade copper oxide in this example comes from an environmental protection company and mainly exists in the form of solid powder. Among them, the copper content of industrial grade copper oxide is 58%, the chlorine content is 0.11%, and the moisture content is 22%.
[0031] Adopt above-mentioned industrial grade copper oxide to prepare the step of industrial grade electroplating copper sulfate as follows, as figure 1 Shown:
[0032] Step Ⅰ: Put 3.5m 3 Tap water was added to the acidification tank, the stirring device was turned on, and 1 t of industrial grade copper oxide was added for mixing and beating, and the reaction was carried out for 10 minutes to obtain a mixed slurry. Dilute and beat industrial copper oxide with tap water, which helps to clean chloride ions and other impurities on the surface of copper oxide, and further makes the acidification reaction more complete.
[0033] Step Ⅱ: First, turn on the exhaust gas absorption system of the aci...
Embodiment 2
[0050] The main component content (mass fraction) of the industrial-grade copper oxide in this embodiment is: copper content 58.38%, chlorine content 0.09%, moisture content 24.37%.
[0051] In this example, the difference from Example 1 is that 3.7m of tap water was added successively in step I 3 , 1t of industrial-grade copper oxide, forming a mass ratio of tap water to industrial-grade copper oxide of 3.7:1.
[0052] In step II, add 98% industrial-grade concentrated sulfuric acid for acidification, adjust the pH of the mixed slurry to 1.4, and maintain the stirring reaction time for 2.5 hours to form a mixed system.
[0053] The pH of the mixed system after the acid supplementation treatment in step III is adjusted to 0.5.
[0054] Refer to Example 1 for the rest of the steps.
[0055] The test indicators of the product after the test are as follows:
[0056] Table 2 Testing indicators of electroplating grade copper sulfate products
[0057]
[0058] As can be known ...
PUM
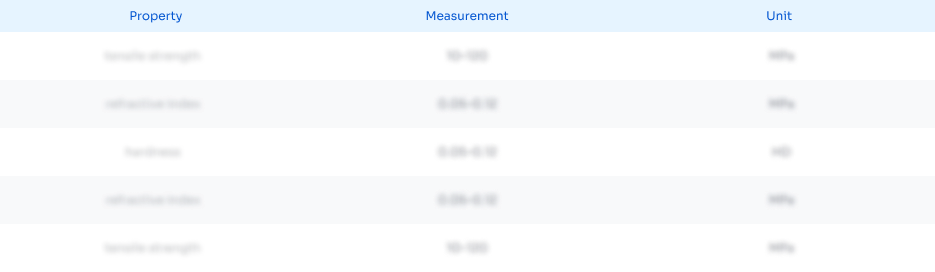
Abstract
Description
Claims
Application Information

- R&D
- Intellectual Property
- Life Sciences
- Materials
- Tech Scout
- Unparalleled Data Quality
- Higher Quality Content
- 60% Fewer Hallucinations
Browse by: Latest US Patents, China's latest patents, Technical Efficacy Thesaurus, Application Domain, Technology Topic, Popular Technical Reports.
© 2025 PatSnap. All rights reserved.Legal|Privacy policy|Modern Slavery Act Transparency Statement|Sitemap|About US| Contact US: help@patsnap.com