Preparation method for polyacrylonitrile-based carbon fiber
A polyacrylonitrile-based carbon fiber and polyacrylonitrile resin technology, which is applied in the fields of fiber chemical characteristics, stretch spinning, single-component synthetic polymer rayon, etc., can solve the problems of raw silk purification and mechanical performance deterioration, etc. Achieve good purification effect and improve mechanical properties
- Summary
- Abstract
- Description
- Claims
- Application Information
AI Technical Summary
Problems solved by technology
Method used
Image
Examples
Embodiment 1~10
[0041] 1) The polyacrylonitrile resin is prepared into a spinning solution by using DMSO as a solvent, and the content of the polyacrylonitrile resin in the spinning solution is 18-25 wt%. Using 30-50wt% DMSO aqueous solution as a coagulation bath to prepare nascent fibers through spinning and coagulation forming by a solution spinning process;
[0042] 2) The as-spun fiber is drawn in a water bath in 20-30 wt% DMSO aqueous solution, and the water bath temperature and the draw ratio of each embodiment are shown in Table 1, and this step is defined as pre-drawing in the table;
[0043] 3) The as-spun fibers are rinsed with deionized water, the water temperature is controlled at 45-60°C, and the rinse time is controlled at 2-20 minutes;
[0044] 4) The as-spun fiber is placed in the acidic aqueous solution for immersion, the control data of the acid and pH value, the temperature of the acidic aqueous solution, bath ratio and immersion time etc. that each embodiment acidic aqueou...
Embodiment 11~12
[0051] 1) The polyacrylonitrile resin is formulated into a spinning solution by using DMAc as a solvent, and the content of the polyacrylonitrile resin in the spinning solution is 18-25 wt%. Using 30-50wt% DMAc aqueous solution as a coagulation bath to prepare nascent fibers through spinning and coagulation forming by a solution spinning process;
[0052] 2) to 9) are the same as in Examples 1 to 10.
Embodiment 13~20、 comparative example 5~6
[0073] Part of the precursors obtained in Examples 1-12 and Comparative Examples 1-4 above were selected to further prepare carbon fibers. The selected precursors are listed in Table 6.
[0074] The raw silk is first pre-oxidized to obtain pre-oxidized silk. The pre-oxidation is carried out in air and is completed in three stages. The oxidation temperature of the first stage is 210-222°C, the oxidation time is 20-24min, and the draw ratio is 0-5; the oxidation temperature of the second stage is 235-245°C. The time is 20~24min, the draw ratio is -1~1; the third oxidation temperature is 255~265℃, the oxidation time is 20~24min, and the draft ratio is -1~1;
[0075] The pre-oxidized silk is further carbonized in nitrogen, and the carbonization is completed in two stages. The carbonization temperature of the first stage is 350-700°C, the carbonization time is 1-2min, and the draw ratio is 3-5 times; the carbonization temperature of the second stage is 800 ~1350℃, the carbonizatio...
PUM
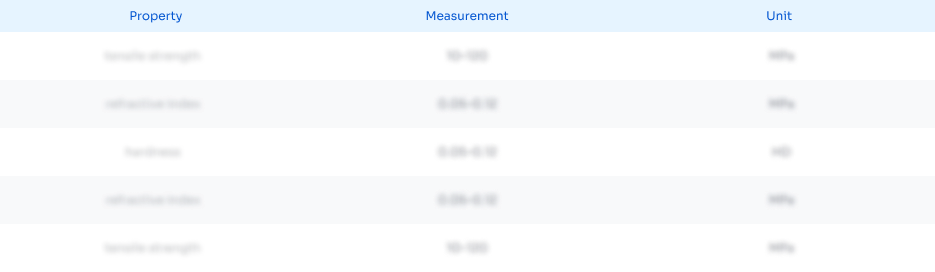
Abstract
Description
Claims
Application Information

- Generate Ideas
- Intellectual Property
- Life Sciences
- Materials
- Tech Scout
- Unparalleled Data Quality
- Higher Quality Content
- 60% Fewer Hallucinations
Browse by: Latest US Patents, China's latest patents, Technical Efficacy Thesaurus, Application Domain, Technology Topic, Popular Technical Reports.
© 2025 PatSnap. All rights reserved.Legal|Privacy policy|Modern Slavery Act Transparency Statement|Sitemap|About US| Contact US: help@patsnap.com