Production process for cogeneration of polymerization ferric chloride water purification agent by using potassium fluotitanate
A technology of polymerizing ferric chloride and potassium fluorotitanate, which is applied in the fields of iron halide, flocculation/sedimentation water/sewage treatment, etc., can solve the problems of high cost of mother liquor treatment, low iron concentration in mother liquor water, and large loss of mother liquor, etc. Good social value and economic value, easy control of operating conditions, and simplified production process effect
- Summary
- Abstract
- Description
- Claims
- Application Information
AI Technical Summary
Problems solved by technology
Method used
Image
Examples
Embodiment 1
[0040] This example uses the following raw materials
[0041] 1. Hydrofluoric acid containing HF 25.3%;
[0042] 2. Potassium chloride contains K 2 O 60.1%;
[0043] 3. Titanium ore (nFe 2 o 3 · mFeO · (3 / 2n+m) T iO 2 ) Contains Ti 29.5%, Fe34.8%, Fe 2 o 3 11.6%, FeO34.3%;
[0044] 4. Refined lime contains CaO73.3%;
[0045] 5. Hydrogen peroxide contains H 2 o 2 20%.
[0046] Specifically include the following steps:
[0047] (1) First add 3000Kg of hydrofluoric acid and 100Kg of potassium chloride into the leaching tank, start stirring, add 1080Kg of titanium ore, seal and continue to react for 2 hours, and the leaching temperature reaches 98°C;
[0048](2) Put the slurry qualified for leaching into the clarification tank with a pump, settle and remove impurities for 16 hours to obtain ferric fluorotitanate clear liquid, the temperature is 51°C;
[0049] (3) Potassium chloride 950 Kg is dissolved with 4000 Kg iron-containing potassium fluotitanate mother liquor ...
Embodiment 2
[0057] This example uses the following raw materials
[0058] 1. Hydrofluoric acid containing 33.2% HF;
[0059] 2. Potassium chloride contains K 2 O 60.1%;
[0060] 3. Titanium ore (nFe 2 o 3 · mFeO · (3 / 2n+m) T iO 2 ) Contains Ti 29.5%, Fe34.8%, Fe 2 o 3 11.6%, FeO34.3%;
[0061] 4. Refined lime contains CaO73.3%;
[0062] 5. Hydrogen peroxide contains H 2 o 2 20%;
[0063] 6. Sodium peroxide contains Na 2 o 2 92.5%.
[0064] Specifically include the following steps:
[0065] (1) First add 2260Kg of hydrofluoric acid and 100Kg of potassium chloride into the leaching tank, start stirring, add 1080Kg of titanium ore, seal and continue to react for 2 hours, and the leaching temperature reaches 100°C;
[0066] (2) Put the slurry qualified for leaching into the clarification tank with a pump, settle and remove impurities for 20 hours to obtain ferric fluorotitanate clear liquid, the temperature is 55°C;
[0067] (3) Potassium chloride 950 Kg is dissolved with 400...
Embodiment 3
[0075] This example uses the following raw materials
[0076] 1. Hydrofluoric acid containing 35.1% HF;
[0077] 2. Potassium chloride contains K 2 O 61.2%;
[0078] 3. Titanium ore (nFe 2 o 3 · mFeO · (3 / 2n+m) T iO 2 ) Contains Ti 30.5%, Fe33.6%, Fe 2 o 3 11.2%, FeO31.3%;
[0079] 4. Refined lime contains CaO73.3%;
[0080] 5. Hydrogen peroxide contains H 2 o 2 20%.
[0081] Specifically include the following steps:
[0082] (1) First add 2130Kg of hydrofluoric acid and 90Kg of potassium chloride into the leaching tank, start stirring, add 1050Kg of titanium ore, seal and continue to react for 2.5 hours, and the leaching temperature reaches 105°C;
[0083] (2) Put the slurry qualified for leaching into the clarification tank with a pump, settle and remove impurities for 8 hours to obtain ferric fluorotitanate clear liquid, the temperature is 58°C;
[0084] (3) Potassium chloride 950 Kg is dissolved with 4000 Kg iron-containing potassium fluotitanate mother liquo...
PUM
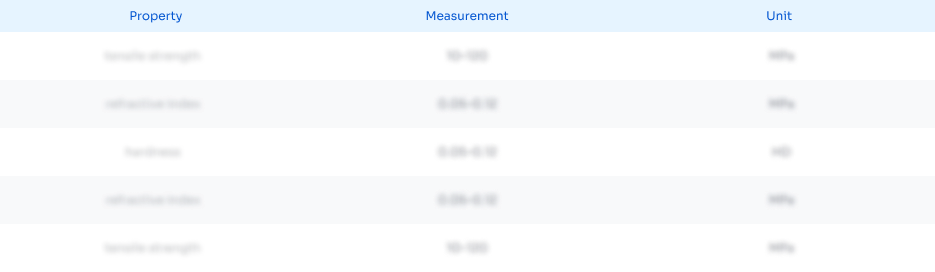
Abstract
Description
Claims
Application Information

- R&D Engineer
- R&D Manager
- IP Professional
- Industry Leading Data Capabilities
- Powerful AI technology
- Patent DNA Extraction
Browse by: Latest US Patents, China's latest patents, Technical Efficacy Thesaurus, Application Domain, Technology Topic, Popular Technical Reports.
© 2024 PatSnap. All rights reserved.Legal|Privacy policy|Modern Slavery Act Transparency Statement|Sitemap|About US| Contact US: help@patsnap.com