Constant-frequency drive method and constant-frequency drive device of tunable micromechanical gyroscope
A technology of a micromachined gyroscope and a driving method, which is applied in the direction of steering induction equipment, etc., can solve the problems of complex control circuits, large delays, and the inability of signal detection circuits to achieve the effect of simplifying signal processing and improving stability.
- Summary
- Abstract
- Description
- Claims
- Application Information
AI Technical Summary
Problems solved by technology
Method used
Image
Examples
Embodiment Construction
[0029] The constant frequency driving method of the tunable micromechanical gyroscope is that the constant frequency driving signal has a constant frequency relative to the reference frequency source, and the phase difference signal between the constant frequency driving signal and the driving mode output signal is obtained through phase difference detection, and the phase difference signal is used to The feedback control obtains the tuning signal, applies the tuning signal to the tuning structure of the tunable micro-mechanical gyro, adjusts the resonant frequency of the driving mode of the tunable micro-mechanical gyroscope, and locks the resonant frequency of the driving mode to the frequency of the constant-frequency driving signal .
[0030] Such as figure 1 As shown, the specific steps of the constant frequency driving method of the tunable micromachined gyroscope are as follows:
[0031] 1) The AC drive signal generation module generates the AC drive signal according t...
PUM
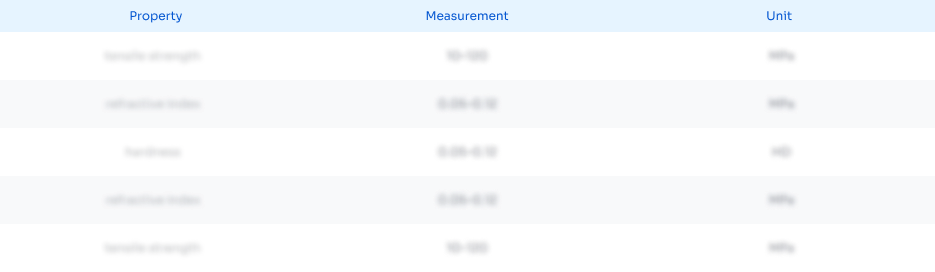
Abstract
Description
Claims
Application Information

- R&D Engineer
- R&D Manager
- IP Professional
- Industry Leading Data Capabilities
- Powerful AI technology
- Patent DNA Extraction
Browse by: Latest US Patents, China's latest patents, Technical Efficacy Thesaurus, Application Domain, Technology Topic, Popular Technical Reports.
© 2024 PatSnap. All rights reserved.Legal|Privacy policy|Modern Slavery Act Transparency Statement|Sitemap|About US| Contact US: help@patsnap.com