Method for preparing o-nitrophenol through phenol nitration selectivity
An o-nitrophenol, selective technology, applied in the field of o-nitrophenol preparation, can solve the problem that the o-nitrophenol content is difficult to exceed 95%, o-nitroanisole is difficult to recycle, and production wastewater treatment is difficult problems such as short preparation period, low cost and high conversion rate of phenol
- Summary
- Abstract
- Description
- Claims
- Application Information
AI Technical Summary
Problems solved by technology
Method used
Image
Examples
Embodiment 1
[0029] Embodiment 1: prepare o-nitrophenol:
[0030] (1) Preparation of catalyst: 1gH 4 PMo 11 VO 40 Dissolve in 9g of deionized water to make 10% H 4 PMo 11 VO 40 Aqueous solution, heated at 50°C for 30min, dissolved 0.091g of cesium carbonate in an appropriate amount of deionized water, and kept at 50°C for 5h to obtain cesium heteropolyacid CsH 3 PMo 11 VO 40 suspension; take 37g (about 39ml) of ethyl silicate, make a solution according to the volume ratio of ethyl silicate: ethanol: water = 1:2:2, heat at 60°C for 30min; Cesium CsH 3 PMo 11 VO 40 The suspension was stirred and added dropwise to the alcohol aqueous solution of ethyl silicate, and continued to heat at 60°C until the gel appeared. After aging for 24 hours, it was dried at 120°C. After drying, 10% cesium heteropolyacid supported on silica was obtained. C 3 PMo 11 VO 40 catalyst.
[0031] (2) Add 0.2mol of phenol to 50ml of 1,2-dichloroethane, add 0.5g of the above catalyst, stir and drop 0.2mol ...
Embodiment 2
[0032] Embodiment 2: prepare o-nitrophenol:
[0033] (1) Preparation of catalyst: 1gH 5 PMo 10 V 2 o 40 Dissolve in 9g of deionized water to make 10% H 4 PMo 10 VO 40 Aqueous solution, heated at 50°C for 30min, dissolved 0.094g of cesium carbonate in an appropriate amount of deionized water, and kept at 40°C for 6h to obtain cesium heteropolyacid CsH 4 PMo 10 V 2 o 40 suspension; take 37g (about 39ml) of ethyl silicate, make a solution by volume ratio of ethyl silicate: ethanol: water = 1:2:2, heat at 80°C for 30min; Cesium CsH 4 PMo 10 V 2 o 40 The suspension was stirred and added dropwise to the alcohol aqueous solution of ethyl silicate, and continued to heat at 80°C until the gel appeared. After aging for 36 hours, it was dried at 110°C. After drying, 10% cesium heteropolyacid supported on silica was obtained. C 4 PMo 10 V 2 o 40 catalyst.
[0034](2) Add 0.2mol of phenol to 50ml of 1,2-dichloroethane, add 1.0g of the above catalyst, stir and drop 0.25mo...
Embodiment 3
[0035] Embodiment 3: prepare o-nitrophenol:
[0036] (1) Preparation of catalyst: 1gH 6 PMo 9 V 3 o 40 Dissolve in 9g of deionized water to make 10% H 6 PMo 9 V 3 o 40 Aqueous solution, heated at 50°C for 30min, dissolved 0.096g of cesium carbonate in an appropriate amount of deionized water, and kept at 60°C for 4h to obtain cesium heteropolyacid CsH 5 PMo 9 V 3 o 40 suspension; take 37g (about 39ml) of ethyl silicate, and make a solution according to the volume ratio of ethyl silicate: ethanol: water = 1:2:2, heat at 70°C for 30min; Cesium CsH 5 PMo 9 V 3 o 40 The suspension was stirred and added dropwise to the alcohol aqueous solution of ethyl silicate, and continued to heat at 70°C until the gel appeared. After aging for 24 hours, it was dried at 100°C. After drying, 10% cesium heteropolyacid supported on silica was obtained. C 5 PMo 9 V 3 o 40 catalyst.
[0037] (2) Add 0.2 mol of phenol to 50 ml of 1,2-dichloroethane, add 1.5 g of the above catalyst,...
PUM
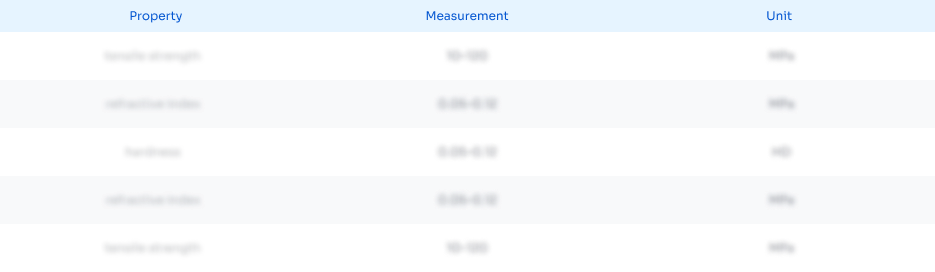
Abstract
Description
Claims
Application Information

- R&D
- Intellectual Property
- Life Sciences
- Materials
- Tech Scout
- Unparalleled Data Quality
- Higher Quality Content
- 60% Fewer Hallucinations
Browse by: Latest US Patents, China's latest patents, Technical Efficacy Thesaurus, Application Domain, Technology Topic, Popular Technical Reports.
© 2025 PatSnap. All rights reserved.Legal|Privacy policy|Modern Slavery Act Transparency Statement|Sitemap|About US| Contact US: help@patsnap.com