Secondary chromeplating process of printing round-net die
A technology for printing rotary screen and mold, applied in jewelry and other directions, can solve the problems of inability to continuously produce, poor uniformity of screen making, short service life, etc., and achieve the effect of not easy to drop glue, high genuine product rate, and lower production cost.
- Summary
- Abstract
- Description
- Claims
- Application Information
AI Technical Summary
Problems solved by technology
Method used
Image
Examples
Embodiment Construction
[0020] The secondary chrome plating process of printing rotary screen mold, the processing steps are as follows:
[0021] 1. Nickel plating operation steps:
[0022] 1). In the mold blank preparation stage, the process of the chrome-plated mold and the nickel-plated mold is the same; the processed mold blank is hoisted into the nickel-plating tank for nickel plating, and the speed is 50-70 rpm;
[0023] 2). According to the number and size of the mold base, set the power on the rectifier to 15-200 ampere hours;
[0024] 3). Start the rectifier, regardless of the size of the mold base, the current is set at 50 amperes;
[0025] 4). After 3-5 minutes of electroplating, increase the current to 150-300 amperes according to the number and size of the mold blank until the electroplating is completed;
[0026] 5) After the electroplating is completed, stop the rotation, lift the mold blank, and rinse the mold blank with pure water;
[0027] Second, the first chrome plating op...
PUM
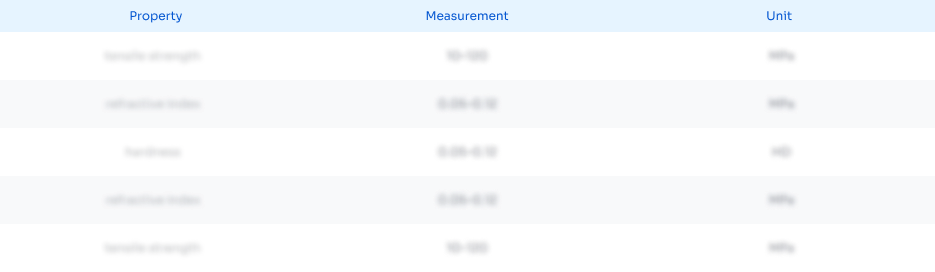
Abstract
Description
Claims
Application Information

- R&D Engineer
- R&D Manager
- IP Professional
- Industry Leading Data Capabilities
- Powerful AI technology
- Patent DNA Extraction
Browse by: Latest US Patents, China's latest patents, Technical Efficacy Thesaurus, Application Domain, Technology Topic, Popular Technical Reports.
© 2024 PatSnap. All rights reserved.Legal|Privacy policy|Modern Slavery Act Transparency Statement|Sitemap|About US| Contact US: help@patsnap.com