Method for preparing silver tin oxide material
A technology of silver tin oxide and raw materials, which is applied in the field of preparation of silver tin oxide materials, can solve the problems of uneven silver tin oxide structure and insufficient oxide content, and achieve stable mass production, sufficient powder oxidation, and short production cycle Effect
- Summary
- Abstract
- Description
- Claims
- Application Information
AI Technical Summary
Problems solved by technology
Method used
Image
Examples
Embodiment 1
[0027] Embodiment 1: 8% tin (percentage by weight), 4% indium (percentage by weight), 0.3% lanthanum (percentage by weight), and silver as the balance are used to form raw materials, which are melted by intermediate frequency at 1250°C and atomized The water pressure is 400MPa, the oxygen flow rate is 6L / min for atomization and oxidation, after separate drying and screening, it is pressed into an ingot under an isostatic pressure of 180MPa, sintered at 850°C for 3 hours, and then sintered at 750°C It is extruded into a plate under temperature conditions, and after surface treatment and silver coating, the plate is rolled, punched and formed, and processed into a sheet contact.
Embodiment 2
[0028] Embodiment 2: According to 10% tin (percentage by weight), 2% indium (percentage by weight), 0.3% lanthanum (percentage by weight), 1.0% bismuth, and the balance is silver, the raw materials are composed, and are smelted by intermediate frequency. 1250°C, atomization water pressure 350MPa, oxygen flow rate 4L / min for atomization and oxidation, separate drying and screening, press into ingot under 220MPa isostatic pressure, sintering at 850°C for 9 hours, Then it is extruded into a wire at a temperature of 800°C, and the wire is drawn and annealed to be processed into a finished wire.
Embodiment 3
[0029] Embodiment 3: According to 12% tin (percentage by weight), 5% indium (percentage by weight), 0.6% lanthanum (percentage by weight), 1.5% bismuth, and the balance is silver, the raw materials are composed, and are smelted by intermediate frequency. 1250°C, atomization water pressure 900MPa, oxygen flow rate 7L / min for atomization and oxidation, separate drying and screening, press into ingot under 220MPa isostatic pressure, sintering at 900°C for 12 hours, Then it is extruded into a wire at a temperature of 880°C, and the wire is drawn and annealed to be processed into a finished wire.
PUM
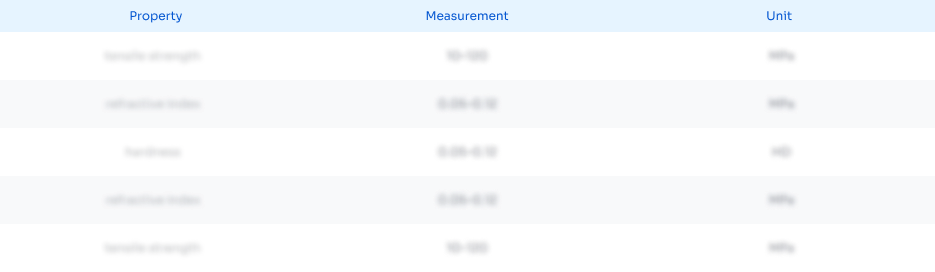
Abstract
Description
Claims
Application Information

- R&D
- Intellectual Property
- Life Sciences
- Materials
- Tech Scout
- Unparalleled Data Quality
- Higher Quality Content
- 60% Fewer Hallucinations
Browse by: Latest US Patents, China's latest patents, Technical Efficacy Thesaurus, Application Domain, Technology Topic, Popular Technical Reports.
© 2025 PatSnap. All rights reserved.Legal|Privacy policy|Modern Slavery Act Transparency Statement|Sitemap|About US| Contact US: help@patsnap.com