Method for enhancing surface abrasion resistance of liquid molding composite material
A technology for liquid forming and composite materials, applied in chemical instruments and methods, synthetic resin layered products, lamination, etc., can solve coating peeling, increase the manufacturing cost of composite structural parts, and interface between surface coatings and composite materials. Weak ability and other problems, to achieve the effect of improving the wear resistance of the surface
- Summary
- Abstract
- Description
- Claims
- Application Information
AI Technical Summary
Problems solved by technology
Method used
Examples
Embodiment 1
[0022] Using benzoxazine resin as matrix resin and high-strength glass fiber satin fabric SW280 as reinforcement, the wear-resistant layer prepreg was prepared by hot-melt method, and the mass fraction of benzoxazine resin was about 40%. Prepolymerize the wear-resistant layer prepreg at 140°C for 3 hours, cool to room temperature, and lay the prepolymerized wear-resistant layer prepreg on the dry carbon fiber preform according to the layering method of [45 / -45]. On the surface of the body, the fiber preform is made of domestic carbon fiber unidirectional lay-up fabric U3160 and laid according to the prescribed laying method. According to the requirements of the liquid molding process, inject a typical aviation high-temperature epoxy resin 5284RTM, and heat up and solidify after the preform is completely infiltrated. Wherein, the injection process parameters and the curing process parameters are the same as the process parameters of the selected resin. After curing, cool to ro...
Embodiment 2
[0024] Using benzoxazine resin as matrix resin and alkali-free glass fiber twill fabric EW250 as reinforcement, the wear-resistant layer prepreg was prepared by hot-melt method, and the resin mass fraction was about 45%. Prepolymerize the wear-resistant layer prepreg at 130°C for 4 hours, cool to room temperature, and lay the prepolymerized layer of wear-resistant prepreg on the surface of the dry carbon fiber preform. The fiber preform is made of domestic carbon fiber The twill fabric CF3031 is laid according to the prescribed laying method. According to the requirements of the liquid molding process, inject typical high-temperature epoxy resin 5284RTM for aviation until the preform is completely infiltrated, and the temperature rises and solidifies. Wherein, the injection process parameters and the curing process parameters are the same as the process parameters of the selected resin. After curing, cool to room temperature and demould. The wear-resistant layer prepreg and ...
Embodiment 3
[0026] Using polyetheretherketone resin as the matrix resin and carbon fiber plain fabric CF3011 as the reinforcing material, the thermoplastic wear-resistant layer prepreg was prepared by electrostatic powder process, and the resin mass fraction was about 40%. A layer of thermoplastic resin wear-resistant layer prepreg is laid on the surface of the dry carbon fiber preform, and the fiber preform is made of domestic carbon fiber satin fabric CF3031 and laid according to the specified layup method. According to the requirements of the liquid molding process, inject typical aviation high-temperature epoxy resin 6421RTM, until the preform is completely infiltrated, and the temperature rises and solidifies. Wherein, the injection process parameters and the curing process parameters are the same as the process parameters of the selected resin. After curing, cool to room temperature and demould. The wear-resistant layer prepreg and the dry carbon fiber preform are co-cured under th...
PUM
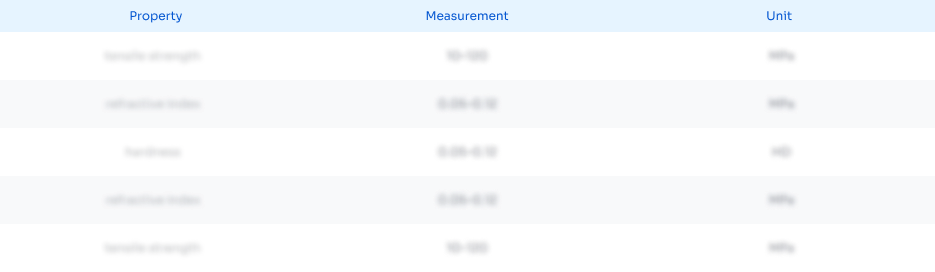
Abstract
Description
Claims
Application Information

- R&D
- Intellectual Property
- Life Sciences
- Materials
- Tech Scout
- Unparalleled Data Quality
- Higher Quality Content
- 60% Fewer Hallucinations
Browse by: Latest US Patents, China's latest patents, Technical Efficacy Thesaurus, Application Domain, Technology Topic, Popular Technical Reports.
© 2025 PatSnap. All rights reserved.Legal|Privacy policy|Modern Slavery Act Transparency Statement|Sitemap|About US| Contact US: help@patsnap.com