Electrolytic method for manufacturing aluminum-manganese alloy in fluoride-chloride molten salt system
A fluoride chloride, magnesium alloy technology, applied in the field of aluminum-magnesium alloy preparation, can solve the problems of difficult recovery, disproportionation reaction and the like
- Summary
- Abstract
- Description
- Claims
- Application Information
AI Technical Summary
Problems solved by technology
Method used
Image
Examples
Embodiment 1
[0016] Example 1: In the electrolytic cell, the inert metal molybdenum (Mo) is used as the cathode and placed in the lower part of the electrolytic cell, graphite is used as the anode, and the mass ratio of each electrolyte in the system is NaCl:KCl:AlF 3 =39%: 50%: 11%, cover and heat to 680°C, after the electrolyte in the crucible melts, add MgCl 2 Added to molten salt, MgCl 2 The amount added is AlF 3 50% of the mass, through direct current electrolysis, at an electrolysis temperature of 680 ° C, the cathode current density is 6.9A / cm 2 , the anode current density is 0.9A / cm 2 , the cell voltage is 5.2~5.6V, after 2.5 hours of electrolysis, Al-Mg alloy is deposited near the cathode in the electrolytic cell. The contents of Al and Mg in the alloy are 94.9% and 5.1%, respectively, and the current efficiency is 55.9%.
Embodiment 2
[0017] Example 2: MgCl 2 The amount added is AlF 3 40% of the mass was electrolyzed by direct current. At an electrolysis temperature of 680°C, the cathode current density was 6.9A / cm2, the anode current density was 0.9A / cm2, and the cell voltage was 4.8-~5.0V. After 4 hours of electrolysis, the The electrolytic cell deposits Al-Mg alloy near the cathode. The contents of Al and Mg in the alloy are 85.3% and 14.7%, respectively, and the current efficiency is 40.5%.
Embodiment 3
[0018] Example 3: MgCl 2 The amount added is AlF 3 40% of the mass, through direct current electrolysis, electrolysis temperature 680 ℃, the cathode current density is 6.9A / cm 2 , the anode current density is 0.9A / cm 2 , the cell voltage is 4.7~4.9V, after 3 hours of electrolysis, Al-Mg alloy is deposited near the cathode in the electrolytic cell. The contents of Al and Mg in the alloy are 84.8% and 15.2%, respectively, and the current efficiency is 49.2%.
PUM
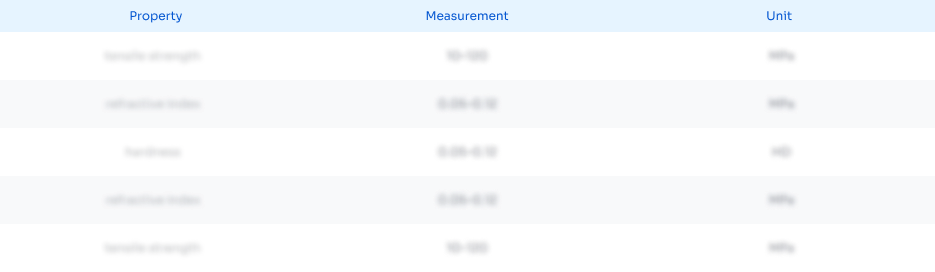
Abstract
Description
Claims
Application Information

- R&D
- Intellectual Property
- Life Sciences
- Materials
- Tech Scout
- Unparalleled Data Quality
- Higher Quality Content
- 60% Fewer Hallucinations
Browse by: Latest US Patents, China's latest patents, Technical Efficacy Thesaurus, Application Domain, Technology Topic, Popular Technical Reports.
© 2025 PatSnap. All rights reserved.Legal|Privacy policy|Modern Slavery Act Transparency Statement|Sitemap|About US| Contact US: help@patsnap.com