Copper-nickel alloy tube preparation method
A copper-nickel alloy tube and tube blank technology, applied in the field of metal processing, can solve the problems of difficult production technology, high dimensional accuracy, and high dimensional deviation, and achieve the effects of excellent plasticity, high flaring manufacturability, and high dimensional deviation accuracy.
- Summary
- Abstract
- Description
- Claims
- Application Information
AI Technical Summary
Problems solved by technology
Method used
Image
Examples
preparation example Construction
[0036] see figure 1 , a method for preparing a copper-nickel alloy tube, comprising the following steps:
[0037] 1) Place the BFe10-1-1 cupronickel material in melting and casting equipment for smelting and casting to obtain an ingot. The composition of the BFe10-1-1 cupronickel material includes: 9.5-10.5% Ni and Co, 1.1-1.3% Fe , 0.58-0.7% Mn, the balance being Cu; the melting temperature is 1280-1330°C, the casting temperature is 1260-1310°C, and the casting speed is 300-400r / min;
[0038] 2) Put the ingot obtained in the above step 1) into an extruder and extrude to obtain a tube blank. The extrusion heating temperature is 850-930°C, the extrusion force is 1350 tons, and the extrusion speed ratio is 20% ;
[0039] 3) Put the tube billet obtained in the above step 2) into a rolling mill for rolling to obtain a coiled tube billet. The rolling pass elongation coefficient of the rolling mill is 3.5-5.0, and the preferred rolling pass The elongation coefficient is 4.51, the...
Embodiment 1
[0044] A method for preparing a copper-nickel alloy tube, comprising the following steps:
[0045] Raw material batching, smelting, pre-furnace analysis, casting, extrusion, rolling, coil drawing, softening annealing of the coiling pass before the finished product, finished product coiling, bright stress relief annealing, coiling and finishing, and finished products. Among them, the chemical composition range of the main elements of the raw material ingredients is shown in Table 1:
[0046] Table 1 BFe10-1-1 main element chemical composition control range
[0047]
[0048] The tensile elongation coefficients are shown in Table 2:
[0049] Table 2 Tensile elongation coefficient
[0050] pass
General intermediate stretching passes
1.2~1.6
Stretching passes to eliminate work hardening
1.7~2.00
The final stretching pass of the finished product
1.05~1.09
[0051] The annealing process parameters are ...
PUM
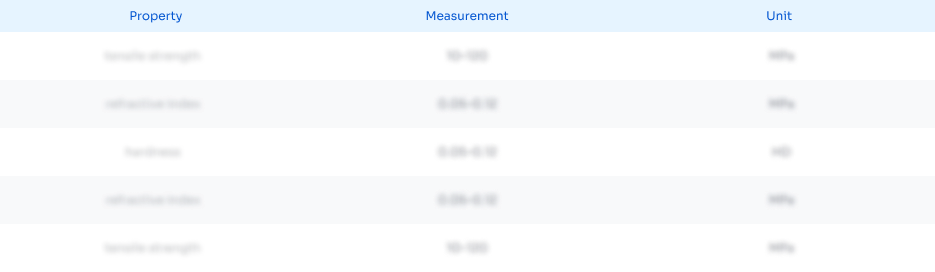
Abstract
Description
Claims
Application Information

- Generate Ideas
- Intellectual Property
- Life Sciences
- Materials
- Tech Scout
- Unparalleled Data Quality
- Higher Quality Content
- 60% Fewer Hallucinations
Browse by: Latest US Patents, China's latest patents, Technical Efficacy Thesaurus, Application Domain, Technology Topic, Popular Technical Reports.
© 2025 PatSnap. All rights reserved.Legal|Privacy policy|Modern Slavery Act Transparency Statement|Sitemap|About US| Contact US: help@patsnap.com