Corrosive for displaying austenitic stainless steel grain boundary of fine grains and method for preparing corrosive
A technology of austenitic stainless steel and fine grains, which is applied in the field of etchant and its preparation, can solve the problems of inconvenient material performance analysis, blurred grain boundaries of etchant, and influence on grain size rating, etc., and achieve good corrosion effect and crystal grain size The effect of clear boundary and little interference of grain boundary
- Summary
- Abstract
- Description
- Claims
- Application Information
AI Technical Summary
Problems solved by technology
Method used
Image
Examples
Embodiment 4
[0034] The Super304H stainless steel alloy composition that adopts in embodiment 4 and comparative example 3 is as shown in table 2:
[0035] Table 2 Test Super304H stainless steel composition (wt%)
[0036] C
Embodiment 1
[0038] Formula: as shown in Table 3
[0039] table 3
[0040] h 2 o
FeCl 3
CuCl 2 2H 2 0
Glacial acetic acid
New Gill
80mL
10mL
15g
10g
2mL
2 drops
[0041] Preparation:
[0042] 10g CuCl 2 2H 2 O is placed in a beaker, and then 15g FeCl is added 3 , then add 10 mL of 36% hydrochloric acid and 80 mL of distilled water, and stir well; finally add 2 mL of glacial acetic acid and 2 drops of neogilamine, and mix well.
[0043] experiment method:
[0044] Process the original fine-grained austenitic TP347HFG stainless steel into a metallographic sample. After polishing, immerse the sample in the above-mentioned corrosive agent for 35 seconds. When the surface is light gray, clean it with water, rinse it with alcohol, and dry it with a hair dryer. Metallographic structure observation with a metallographic microscope, such as figure 1 shown.
Embodiment 2
[0046] Formula: as shown in Table 4
[0047] Table 4
[0048] h 2 o
FeCl 3
CuCl 2 2H 2 o
Glacial acetic acid
New Gill
100mL
15mL
18g
12g
5mL
4 drops
[0049] Preparation:
[0050] 12g CuCl 2 2H 2 O is placed in a beaker, and then 18g FeCl is added 3 , then add 15 mL of 36% hydrochloric acid and 100 mL of distilled water, and stir well; finally add 5 mL of glacial acetic acid and 4 drops of neogilamine, and mix well.
[0051] experiment method:
[0052] The original state, heat treatment for 10 minutes (heat treatment method: heat up to 950°C and then keep it for 10 minutes, air cool to room temperature), 20 minutes heat treatment (heat treatment method: heat up to 950°C and then hold for 20 minutes, air cool to room temperature) fine grains Austenitic TP347HFG stainless steel is processed into a metallographic sample. After polishing, the sample is immersed in the above-mentioned cor...
PUM
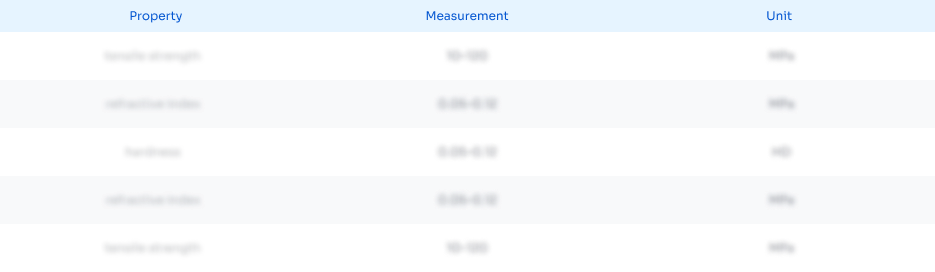
Abstract
Description
Claims
Application Information

- R&D Engineer
- R&D Manager
- IP Professional
- Industry Leading Data Capabilities
- Powerful AI technology
- Patent DNA Extraction
Browse by: Latest US Patents, China's latest patents, Technical Efficacy Thesaurus, Application Domain, Technology Topic, Popular Technical Reports.
© 2024 PatSnap. All rights reserved.Legal|Privacy policy|Modern Slavery Act Transparency Statement|Sitemap|About US| Contact US: help@patsnap.com