Combined-type SVPWM method
A modulation method and combined technology, applied in control systems, control generators, vector control systems, etc., can solve the problems of large inverter generation, large inverter losses, and low efficiency of motor drive systems.
- Summary
- Abstract
- Description
- Claims
- Application Information
AI Technical Summary
Problems solved by technology
Method used
Image
Examples
Embodiment Construction
[0046] According to the different modulation principles of seven-segment SVPWM, flat-top SVPWM, half-frequency SVPWM, and FFC SVPWM, in the simulation software (such as Matlab software equipped with Simulink toolkit, etc.), the four SVPWM methods are tested in each permanent magnet synchronous motor. The electromagnetic torque fluctuation at the operating point (at different speeds and different torques) is compared with the loss of power switching devices (such as diodes, IGBT devices, etc.), and the simulation results are shown in the following four tables.
[0047]
[0048]
[0049] Table 2 Original simulation results under small torque
[0050]
[0051]
[0052] Table 3 Original simulation results under medium torque
[0053]
[0054] Table 4 Original simulation results under high torque
[0055]
[0056]
[0057] Table 5 The original simulation results of seven-segment and FFC
[0058] see Figure 11 to Figure 13 , are the actual electromagnetic to...
PUM
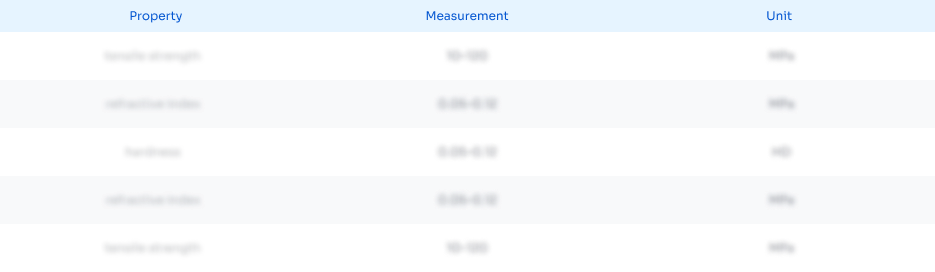
Abstract
Description
Claims
Application Information

- R&D
- Intellectual Property
- Life Sciences
- Materials
- Tech Scout
- Unparalleled Data Quality
- Higher Quality Content
- 60% Fewer Hallucinations
Browse by: Latest US Patents, China's latest patents, Technical Efficacy Thesaurus, Application Domain, Technology Topic, Popular Technical Reports.
© 2025 PatSnap. All rights reserved.Legal|Privacy policy|Modern Slavery Act Transparency Statement|Sitemap|About US| Contact US: help@patsnap.com