Method for enhancing damping capacity of rubber by adding samarium-cobalt magnetic powder
A technology of samarium cobalt and magnetic powder, which is applied in the field of improving the damping performance of rubber by adding samarium cobalt magnetic powder, which can solve the problems of rising cost and declining magnetic performance, and achieve the effects of increasing energy conversion, increasing the effective damping temperature range, and improving damping performance
- Summary
- Abstract
- Description
- Claims
- Application Information
AI Technical Summary
Problems solved by technology
Method used
Image
Examples
Embodiment 1
[0028] 1) Plasticize 100 parts by mass of butyl rubber on an open mill, then add 50 parts by mass of carbon black reinforcing agent, 20 parts by mass of isotropic fast-quenching samarium cobalt magnetic powder with a particle size of 100 microns, 2 parts by mass Sulfur, 5 parts by mass of zinc oxide, and 1.5 parts by mass of stearic acid were kneaded for 5 minutes to obtain a mixture;
[0029] 2) Put the mixture in the mold, apply a pressure of 5 Pa to the mold, and keep it at 120°C for 30 minutes for vulcanization to obtain vulcanized rubber;
[0030] 3) Place the vulcanized rubber under a 5T magnetic field for 1 second to obtain high-damping samarium-cobalt magnetic rubber.
[0031] Compared with ordinary butyl rubber, the maximum damping coefficient of samarium cobalt magnetic rubber with 20 mass parts of magnetic powder increased from 0.85 to 0.98 at 50, an increase of 15%, and the damping performance was significantly improved.
Embodiment 2
[0033] 1) Plasticize 100 parts by mass of nitrile rubber on a calender, then add 35 parts by mass of carbon black reinforcing agent, 120 parts by mass of anisotropic fast-quenching samarium-cobalt magnetic powder with a particle size of 1 micron, and 1.5 parts by mass of sulfur , 5 parts by mass of zinc oxide, 1 part by mass of stearic acid, mixed for 5 minutes to obtain a mixture;
[0034] 2) Put the mixture in the mold, apply a pressure of 15Pa to the mold, and keep it at 150°C for 10 minutes for vulcanization to obtain vulcanized rubber;
[0035] 3) Place the vulcanized rubber under a 4T magnetic field for 5 seconds to obtain a high-damping samarium-cobalt magnetic rubber.
[0036] Compared with ordinary butyl rubber, the maximum damping coefficient of samarium cobalt magnetic rubber with 60 mass parts of magnetic powder increased from 0.84 to 1.05 at 50, an increase of 25%, and the damping performance was significantly improved.
Embodiment 3
[0038] 1) Plasticize 100 parts by mass of silicone rubber on a mixer, then add 50 parts by mass of white carbon black reinforcing agent, 60 parts by mass of isotropic injection-molded samarium-cobalt magnetic powder with a particle size of 70 microns, and 0.8 parts by mass of sulfur, Mix for 15 minutes to obtain a mixture;
[0039] 2) Put the mixture in the mold, apply a pressure of 20Pa to the mold, and keep it at 170°C for 20 minutes for vulcanization to obtain vulcanized rubber;
[0040] 3) Place the vulcanized rubber under a 1.5T magnetic field for 10 seconds to obtain a high-damping samarium-cobalt magnetic rubber.
[0041] Compared with ordinary silicone rubber, the maximum damping coefficient of samarium cobalt magnetic rubber with 120 mass parts of magnetic powder increased from 0.34 to 0.40 at 50, an increase of 18%, and the damping performance was significantly improved.
PUM
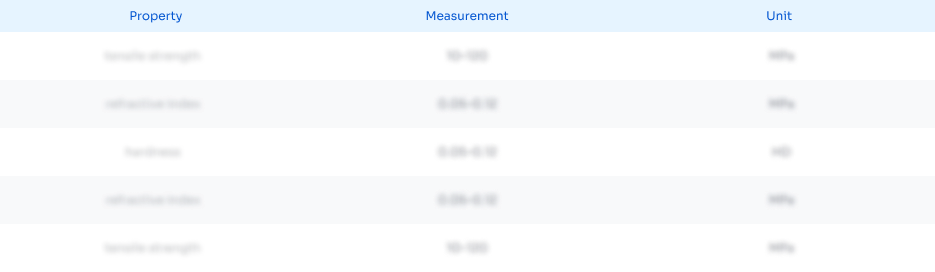
Abstract
Description
Claims
Application Information

- R&D Engineer
- R&D Manager
- IP Professional
- Industry Leading Data Capabilities
- Powerful AI technology
- Patent DNA Extraction
Browse by: Latest US Patents, China's latest patents, Technical Efficacy Thesaurus, Application Domain, Technology Topic, Popular Technical Reports.
© 2024 PatSnap. All rights reserved.Legal|Privacy policy|Modern Slavery Act Transparency Statement|Sitemap|About US| Contact US: help@patsnap.com