Method for efficiently extracting fossilized plant wax from brown coal and device thereof
A high-efficiency, vegetable wax technology, applied in the field of coal chemical industry, can solve the problems of high extraction temperature and pressure conditions, high labor intensity of workers, and poor quality of montan wax, etc., to achieve high equipment utilization efficiency, equipment volume reduction, automation high degree of effect
- Summary
- Abstract
- Description
- Claims
- Application Information
AI Technical Summary
Problems solved by technology
Method used
Image
Examples
Embodiment approach
[0031] The organic solvent is a mixed solvent of toluene and ethanol or tert-butanol, the volume ratio of toluene in the mixed solvent is 80-95%, and the volume ratio of ethanol or tert-butanol is 5-20%.
[0032] The qualified particle size coal is sent to the heat exchanger 3 through the feeding scraper machine 1, and after being preheated to 85-95°C, it is sent to the ring-belt-frame leaching machine 7 by the distribution scraper machine 5 for leaching. You can also choose the star feeder to be used in conjunction with or replace the scraper conveying device.
[0033] The waxy organic solvent is preheated to 85~95°C by the heat exchanger 15, and then sprayed onto the coal particles in the belt-frame leaching machine 7; the primary waxy organic solvent of the waxy organic solvent is The concentration is 1.5-2.5%, and then the waxy concentration is gradually decreased with a gradient of 0.15-0.25%, until the residual coal after leaching is washed with pure organic solvent.
...
Embodiment 1
[0042] Raw coal is crushed and screened to obtain coal with a particle size of 0.2-5.0mm, and the base moisture of the coal is controlled to be 16-20% after drying. After preheating to 85°C, the coal with qualified particle size is sent to the belt-frame leaching machine 7, and it is contacted and mass-transferred with the waxy organic solvent preheated to 85°C. The organic solvent includes volume ratio A mixed solvent of 80% toluene and 20% ethanol; the wax concentration in the initial waxy organic solvent is 1.5%, and then the wax concentration gradually decreases with a gradient of 0.15% until the residual coal after leaching is washed with pure organic solvent ; After the pure organic solvent is preheated to 85°C, spray and wash the residual coal after leaching according to the weight ratio of coal and organic solvent 1:1.5, and remove the residual wax in the coal to a dry wax content of E B,d <0.8%, then the residual coal enters the 1.5m-long draining section to drain the...
Embodiment 2
[0044] Raw coal is crushed and screened to obtain coal with a particle size of 0.2-5.0mm, and the base moisture of the coal is controlled to be 16-20% after drying. Preheat coal with qualified particle size to 95°C and send it into the belt-frame leaching machine 7, and contact with the wax-containing organic solvent preheated to 95°C for countercurrent mass transfer, and the organic solvent includes volume ratio A mixed solvent of 95% toluene and 5% ethanol; the wax concentration in the primary waxy organic solvent is 2.5%, and the wax concentration gradually decreases with a gradient of 0.25% until the residual coal after leaching is washed with pure organic solvent; After the pure organic solvent is preheated to 95°C, the residual coal after leaching is sprayed and washed according to the weight ratio of coal and organic solvent 1:2.5, and the residual wax in the coal is removed to a dry wax content of E B,d <0.8%, then the residual coal enters the 2.5m-long draining sectio...
PUM
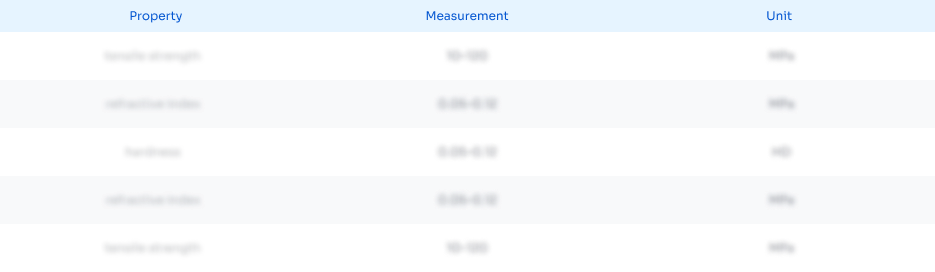
Abstract
Description
Claims
Application Information

- Generate Ideas
- Intellectual Property
- Life Sciences
- Materials
- Tech Scout
- Unparalleled Data Quality
- Higher Quality Content
- 60% Fewer Hallucinations
Browse by: Latest US Patents, China's latest patents, Technical Efficacy Thesaurus, Application Domain, Technology Topic, Popular Technical Reports.
© 2025 PatSnap. All rights reserved.Legal|Privacy policy|Modern Slavery Act Transparency Statement|Sitemap|About US| Contact US: help@patsnap.com