Synthetic technology of graphite oxide
A synthesis process, graphite technology, applied in the direction of graphite, etc., can solve the problems of large consumption of raw materials, cumbersome operation steps, unsuitable for industrial production, etc., and achieve the effect of high raw material utilization rate, wide application prospect, and simple preparation process
- Summary
- Abstract
- Description
- Claims
- Application Information
AI Technical Summary
Problems solved by technology
Method used
Image
Examples
Embodiment 1
[0016] Embodiment 1: Prepare graphite oxide with natural graphite as raw material. Weigh 10.00g of graphite powder and place it in a beaker, add 100ml of concentrated sulfuric acid, 10.00g of sodium persulfate and 10.00g of vanadium pentoxide and stir, ultrasonically treat for 5min, then mechanically stir for 6h in a water bath at 80°C, and let stand for 9h. After filtering and drying, add 500ml of concentrated sulfuric acid, ultrasonic treatment for 30min, slowly add 60.00g of potassium permanganate, then continue mechanical stirring for 4h, add 500ml of deionized water under ice-cooling condition, stir for another 2h, and finally add hydrogen peroxide , Stir while adding until no bubbles emerge to obtain a graphite oxide solution. The graphite oxide solution is filtered and dried to obtain graphite oxide. The prepared graphite oxide has an oxygen content of 38 wt% and an interlayer distance of 0.67 nm.
Embodiment 2
[0017] Example 2: Graphite oxide was prepared from flake graphite as raw material. Weigh 5.00g of graphite powder and place it in a beaker, add 60ml of concentrated sulfuric acid, 5.00g of potassium persulfate and 6.00g of phosphorus pentoxide and stir, ultrasonically treat for 3min, then mechanically stir for 2h in a water bath at 20°C, and let stand for 10h. After filtering and drying, then add 250ml of concentrated sulfuric acid, ultrasonic treatment for 3min, slowly add 35.00g of potassium permanganate, then continue to mechanically stir for 2h, add 250ml of deionized water under ice-cooling conditions, stir for 0.5h, and finally add Add hydrogen peroxide and stir until no bubbles emerge to obtain a graphite oxide solution. The graphite oxide solution is filtered and dried to obtain graphite oxide. The prepared graphite oxide has an oxygen content of 47 wt% and an interlayer distance of 0.70 nm.
Embodiment 3
[0018] Embodiment 3: Prepare graphite oxide by using earthy graphite as raw material. Weigh 20.00g of graphite powder and place it in a beaker, add 240ml of concentrated sulfuric acid, 24.00g of sodium persulfate and 24.00g of phosphorus trioxide and stir, ultrasonically treat for 10min, then mechanically stir for 8h in an oil bath at 100°C, and let stand for 16h. After filtering and drying, then add 1000ml of concentrated sulfuric acid, ultrasonic treatment for 50min, slowly add 120.00g of potassium permanganate, continue mechanical stirring for 3h, add 1000ml of deionized water under ice cooling conditions, stir for 8h, and finally add hydrogen peroxide, Stir while adding until no bubbles emerge to obtain a graphite oxide solution. The graphite oxide solution is filtered and dried to obtain graphite oxide. The prepared graphite oxide has an oxygen content of 53 wt% and an interlayer distance of 0.75 nm.
PUM
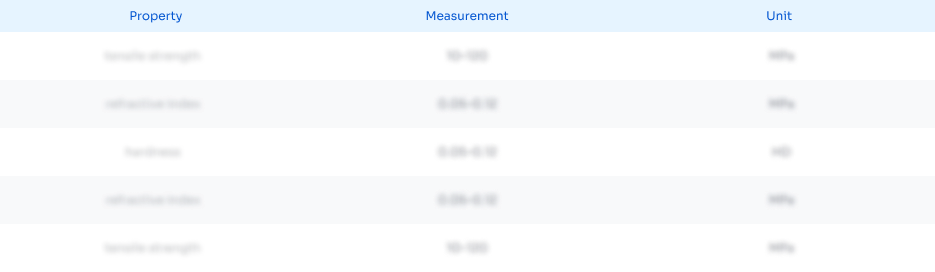
Abstract
Description
Claims
Application Information

- R&D Engineer
- R&D Manager
- IP Professional
- Industry Leading Data Capabilities
- Powerful AI technology
- Patent DNA Extraction
Browse by: Latest US Patents, China's latest patents, Technical Efficacy Thesaurus, Application Domain, Technology Topic, Popular Technical Reports.
© 2024 PatSnap. All rights reserved.Legal|Privacy policy|Modern Slavery Act Transparency Statement|Sitemap|About US| Contact US: help@patsnap.com