Preparation method of lithium titanate material, lithium titanate material, and lithium ion battery
A lithium titanate, lithium source technology, applied in battery electrodes, secondary batteries, circuits, etc., can solve problems such as poor rate discharge performance
- Summary
- Abstract
- Description
- Claims
- Application Information
AI Technical Summary
Problems solved by technology
Method used
Image
Examples
preparation example Construction
[0011] The preparation method of the lithium titanate material disclosed in the present invention comprises the steps of preliminary ball milling the mixture containing the lithium source and the nickel source, and then performing preliminary calcination to obtain a precursor; then mixing the precursor with the titanium source and performing secondary ball milling, and then Secondary calcination is carried out in an inert atmosphere or a reducing atmosphere to obtain the lithium titanate material.
[0012] According to the present invention, the lithium source adopted in the above method can adopt various lithium salts in the prior art, for example, the lithium source can be selected from lithium hydroxide, lithium acetate, lithium carbonate, lithium chloride, lithium chromate, One or more of lithium citrate, lithium tetrachloroaluminate, lithium bromide, lithium tetrafluoroborate or lithium oxalate.
[0013] As a doping element, the nickel source disclosed in the present inve...
Embodiment 1
[0043] This embodiment is used to illustrate the lithium titanate material disclosed in the present invention, its preparation method and lithium ion battery.
[0044] Preparation of lithium titanate material: 0.8 mol of lithium carbonate was mixed with 0.0008 mol of nickel oxide to obtain a mixture. The mixture was then ball milled in a ball mill for 5 h, and then preliminarily calcined at 600 °C for 5 h. get the precursor. The precursor was mixed with 1 mol of titanium oxide and milled twice in a ball mill for 5 h. The product of the secondary ball milling was then calcined at 600° C. for 24 hours in a nitrogen atmosphere to obtain the lithium titanate material A1.
[0045] Preparation of non-aqueous electrolyte: Mix ethylene carbonate (EC), ethyl methyl carbonate (EMC), and dimethyl carbonate (DMC) in a volume ratio of 3:3:2, and add lithium salt LiPF 6 , with a concentration of 1 mol / l, and stirred evenly to obtain an electrolyte solution.
[0046] Preparation of negat...
Embodiment 2
[0050] This embodiment is used to illustrate the lithium titanate material disclosed in the present invention, its preparation method and lithium ion battery.
[0051] 0.81 mol of lithium chloride was mixed with 0.0405 mol of nickel carbonate to obtain a mixture. The mixture was then ball milled in a ball mill for 6 h, and then preliminarily calcined at 650 °C for 6 h. get the precursor. The precursor was mixed with 1 mol of titanium oxide and milled twice in a ball mill for 6 h. The product of the secondary ball milling was then calcined for a second time at 750° C. for 12 hours in a nitrogen atmosphere to obtain the lithium titanate material A2.
[0052] The lithium-ion battery S2 was prepared by using the above-mentioned lithium titanate material A2 according to the method of Example 1.
PUM
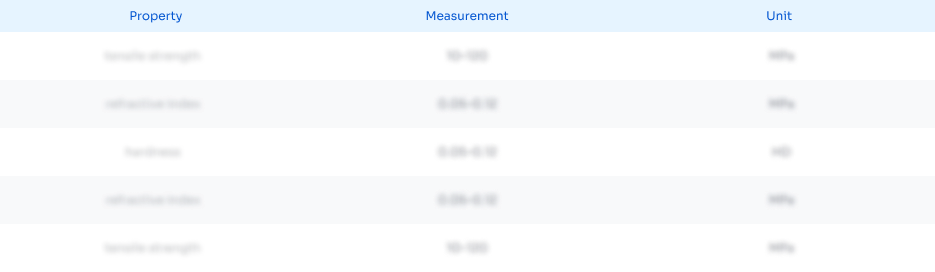
Abstract
Description
Claims
Application Information

- Generate Ideas
- Intellectual Property
- Life Sciences
- Materials
- Tech Scout
- Unparalleled Data Quality
- Higher Quality Content
- 60% Fewer Hallucinations
Browse by: Latest US Patents, China's latest patents, Technical Efficacy Thesaurus, Application Domain, Technology Topic, Popular Technical Reports.
© 2025 PatSnap. All rights reserved.Legal|Privacy policy|Modern Slavery Act Transparency Statement|Sitemap|About US| Contact US: help@patsnap.com