A production process of breathable and cashmere-proof fine denier fabric
A production process and fabric technology, applied in the field of weaving and dyeing of textiles, to achieve the effect of improving the anti-down property, the feel of the down-proof fabric, and the good feel of the fabric
- Summary
- Abstract
- Description
- Claims
- Application Information
AI Technical Summary
Problems solved by technology
Method used
Image
Examples
Embodiment 1
[0025] A production process of air-permeable and cashmere-proof fine denier fabric, which is carried out as follows: gray cloth weaving→cold pile treatment→desizing→dyeing→setting→water washing→calendering, in which: the warp and weft of the gray cloth are all made of 20D nylon matting FDY Filament, warp direction density 78 / cm, weft density 78 / cm.
[0026] Cold-stack treatment is to dip the gray cloth in the cold-stack padding solution in the padding tank of the padding car for padding treatment, then wrap and seal it, and stack the sealed cloth rolls on the cold-stack rack for 24 hours, while keeping the cloth The roll rotates slowly at a speed of 16m / min; the padding liquid in the padding tank is made of H 2 o 2 , NaOH, and refining agent are mixed at a weight ratio of 10:20:2, and an aqueous solution prepared by adding 30 times the total weight of the three deionized water, wherein the refining agent is refining agent TK-1.
[0027] Loose open-width desizing is used for ...
Embodiment 2
[0033] A production process of air-permeable and cashmere-proof fine denier fabric, which is carried out as follows: gray cloth weaving→cold pile treatment→desizing→dyeing→setting→water washing→calendering, in which: the warp and weft of the gray cloth are all made of 20D nylon matting FDY Filament, warp direction density 78 / cm, weft density 78 / cm.
[0034] Cold-stack treatment is to dip the gray cloth in the cold-stack padding solution in the padding tank of the padding car for padding treatment, then wrap and seal it, and stack the sealed cloth rolls on the cold-stack rack for 24 hours, while keeping the cloth The roll rotates slowly at a speed of 17m / min; the padding liquid in the padding tank is made of H 2 o 2 , NaOH, and refining agent are mixed in a weight ratio of 10:20:2, and an aqueous solution prepared by adding 31 times the total weight of the three deionized water is prepared, wherein the refining agent is refining agent TK-1.
[0035] Loose open-width desizing ...
Embodiment 3
[0041] A production process of air-permeable and cashmere-proof fine denier fabric, which is carried out as follows: gray cloth weaving→cold pile treatment→desizing→dyeing→setting→water washing→calendering, in which: the warp and weft of the gray cloth are all made of 20D nylon matting FDY Filament, warp direction density 78 / cm, weft density 78 / cm.
[0042] Cold-stack treatment is to dip the gray cloth in the cold-stack padding solution in the padding tank of the padding car for padding treatment, then wrap and seal it, and stack the sealed cloth rolls on the cold-stack rack for 24 hours, while keeping the cloth The roll rotates slowly at a speed of 16m / min; the padding liquid in the padding tank is made of H 2 o 2 , NaOH, and refining agent in a weight ratio of 10:20:2, and add 33 times the total weight of the three deionized water to prepare an aqueous solution, wherein the refining agent is refining agent TK-1.
[0043] Loose open-width desizing is used for desizing, and ...
PUM
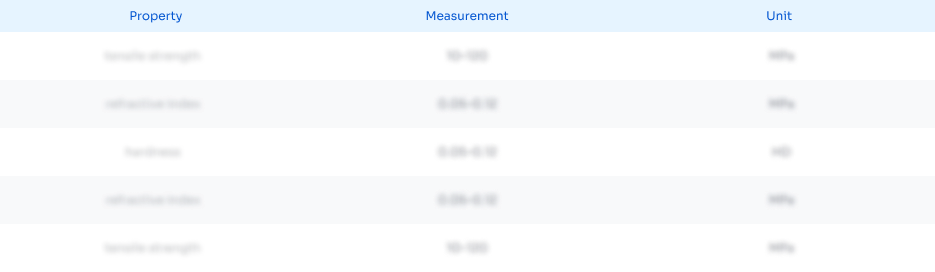
Abstract
Description
Claims
Application Information

- Generate Ideas
- Intellectual Property
- Life Sciences
- Materials
- Tech Scout
- Unparalleled Data Quality
- Higher Quality Content
- 60% Fewer Hallucinations
Browse by: Latest US Patents, China's latest patents, Technical Efficacy Thesaurus, Application Domain, Technology Topic, Popular Technical Reports.
© 2025 PatSnap. All rights reserved.Legal|Privacy policy|Modern Slavery Act Transparency Statement|Sitemap|About US| Contact US: help@patsnap.com