Long glass fiber-reinforced polyvinyl chloride sheet as well as preparation method of on-line mixing of polyvinyl chloride sheet
A polyvinyl chloride and long glass fiber technology, which is applied in the field of plastic product processing, can solve the problems of high melt viscosity, poor fluidity, and difficult processing.
- Summary
- Abstract
- Description
- Claims
- Application Information
AI Technical Summary
Problems solved by technology
Method used
Image
Examples
Embodiment 1
[0026] Feed 100 parts of PVC (K value: 66) into the first zone of the first-stage co-rotating twin-screw extruder, add additives (including 2 parts of mercaptan dibutyltin, 1 part of calcium stearate, stearate Zinc acid 0.5 parts, butyl stearate 2 parts, higher fatty acid 2 parts, paraffin wax 0.5 parts, high melting point oxidized polyethylene 0.5 parts, PE-g-MAH 3 parts) After fully mixing, feed the first stage co-rotating twin-screw In the second zone of the extruder, the activated calcium carbonate is fed into the sixth zone of the first-stage co-rotating twin-screw extruder, and 10 parts of glass fiber non-twisted roving are introduced into the coupling agent KH550 infiltration tank on the surface treatment machine, and wound around 6 The hot roller (110°C) stays for 10 minutes, then feeds into the third zone of the second-stage twin-screw extruder, extrudes from the coat-hanger die of the second-stage twin-screw extruder (head pressure 8MPa), and then is calendered by thr...
Embodiment 2
[0028] Feed 100 parts of PVC (K value: 68) into the first zone of the first-stage co-rotating twin-screw extruder, add additives (including 2.5 parts of mercaptan dibutyltin, 0.5 parts of calcium stearate, stearate Zinc acid 0.3 part, butyl stearate 1 part, higher fatty acid 1 part, paraffin wax 1 part, high-melting point oxidized polyethylene 1 part, PE-g-MAH 4 parts) fully mixed, fed into the first stage of the same direction In the second zone of the screw extruder, the activated calcium carbonate is fed into the sixth zone of the first-stage co-rotating twin-screw extruder. 20 parts of glass fiber non-twist roving are introduced into the coupling agent KH550 soaking tank on the surface treatment machine, and the warp 6 hot rollers (110°C) stay for 10 minutes, then feed into the third zone of the second-stage twin-screw extruder, extrude from the second-stage twin-screw extruder coat hanger die (head pressure 8MPa), and then pass through the three-roller Calendering, shapin...
Embodiment 3
[0030] Feed 100 parts of PVC (K value: 70) into the first zone of the first-stage co-rotating twin-screw extruder, add additives (including 3 parts of mercaptan dibutyltin, 0.4 parts of calcium stearate, stearate Zinc acid 0.4 parts, butyl stearate 2 parts, higher fatty acid 2 parts, paraffin 1 part, high melting point oxidized polyethylene 0.8 parts, PE-g-MAH 3 parts) After fully mixing, feed the first stage co-rotating twin-screw In the second zone of the extruder, activated calcium carbonate is fed into the sixth zone of the first-stage co-rotating twin-screw extruder. 30 parts of glass fiber no-twisted roving are introduced into the infiltration tank of coupling agent KH550 on the surface treatment machine, and wound by 6 The hot roller (110°C) stays for 10 minutes, then feeds into the third zone of the second-stage twin-screw extruder, extrudes from the coat-hanger die of the second-stage twin-screw extruder (head pressure 8MPa), and then is calendered by three rollers , ...
PUM
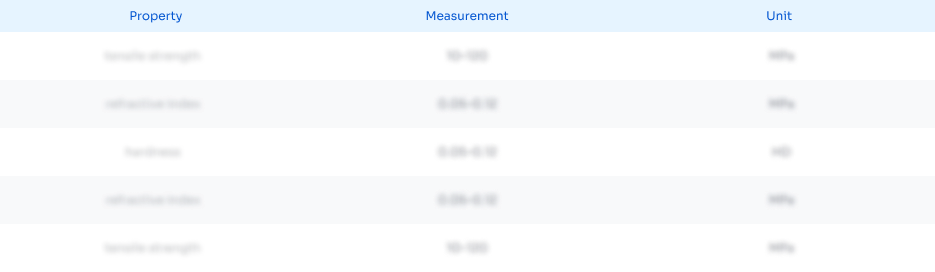
Abstract
Description
Claims
Application Information

- Generate Ideas
- Intellectual Property
- Life Sciences
- Materials
- Tech Scout
- Unparalleled Data Quality
- Higher Quality Content
- 60% Fewer Hallucinations
Browse by: Latest US Patents, China's latest patents, Technical Efficacy Thesaurus, Application Domain, Technology Topic, Popular Technical Reports.
© 2025 PatSnap. All rights reserved.Legal|Privacy policy|Modern Slavery Act Transparency Statement|Sitemap|About US| Contact US: help@patsnap.com