In-groove type helical milling method
A processing method and groove feature technology, applied in the processing field of mechanical parts, can solve the problems of low efficiency, manual grinding, and difficulty in ensuring accuracy, and achieve the effects of fast processing speed, improved quality and stable load
- Summary
- Abstract
- Description
- Claims
- Application Information
AI Technical Summary
Problems solved by technology
Method used
Image
Examples
Embodiment Construction
[0039] The present invention will be further described below in conjunction with the accompanying drawings and embodiments.
[0040] Such as Figure 1-6 shown.
[0041] A method for helical milling of groove feature inner profile, which comprises the following steps:
[0042] Step 1. Input the groove feature internal shape part into the CAM software system to preprocess the part. The input of the part feature information is to read the feature information list of the part, or to obtain the drive related to the internal shape by manually clicking on the feature of the part Geometry, and then extract the internal tool path to generate the driving line according to the driving geometry; the relevant driving geometry of the spiral tool path milling internal shape includes corner surfaces, side surfaces, top surfaces, and web surfaces, and discretize the driving lines to form the underlying discrete points;
[0043] Step 2, offset the bottom discrete point to the top surface of t...
PUM
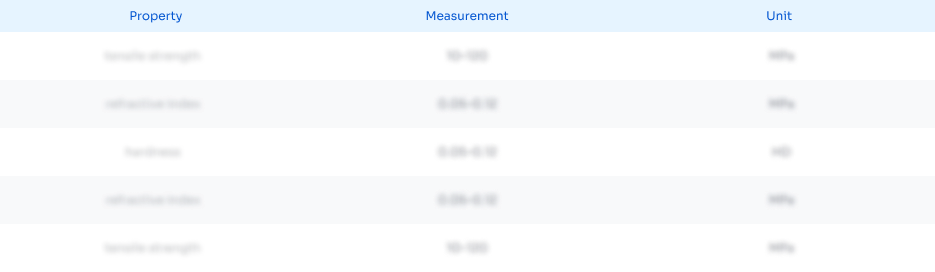
Abstract
Description
Claims
Application Information

- R&D
- Intellectual Property
- Life Sciences
- Materials
- Tech Scout
- Unparalleled Data Quality
- Higher Quality Content
- 60% Fewer Hallucinations
Browse by: Latest US Patents, China's latest patents, Technical Efficacy Thesaurus, Application Domain, Technology Topic, Popular Technical Reports.
© 2025 PatSnap. All rights reserved.Legal|Privacy policy|Modern Slavery Act Transparency Statement|Sitemap|About US| Contact US: help@patsnap.com