Preparation method for electricity conductive cloth, and electricity conductive cloth
A technology of conductive cloth and original cloth, applied in the field of conductive cloth, can solve the problems of high investment and low yield of conductive cloth preparation process, and achieve the effects of high yield, low product resistance and excellent adhesion
- Summary
- Abstract
- Description
- Claims
- Application Information
AI Technical Summary
Problems solved by technology
Method used
Examples
Embodiment 1
[0034] Embodiment 1 280T polyurethane fiber grid cloth
[0035] Using 280T polyurethane fiber grid cloth as the original cloth, the original cloth is dip-coated in the catalytic liquid mixed with palladium salt and PU resin solution at room temperature. The solid content of PU resin in the catalytic liquid is 0.4%, and the palladium content is 320ppm. After pressing, enter the oven for drying and curing at 200 degrees Celsius.
[0036] Electroless copper plating is performed on the catalyzed original fabric, so that the surface of the original fabric fiber is plated with a conductive chemical copper layer. Wherein, the electroless copper plating liquid that adopts in the described electroless copper plating process mainly contains the copper chloride that concentration is 7.5g / L, the EDTA of 30g / L, the NaOH of 10g / L, the HCHO of 4g / L and a small amount of chemical copper Stabilizer, the plating temperature is controlled at 40 degrees Celsius. The chemical copper stabilizer i...
Embodiment 2
[0039] Embodiment 2 270T polyurethane fiber grid cloth
[0040] 270T polyurethane fiber grid cloth is used as the original cloth, and the original cloth is dip-coated in the catalytic liquid mixed with palladium salt and PU resin solution at room temperature. The solid content of PU resin in the catalytic liquid is 0.6%, and the palladium content is 330ppm. After pressing, enter the oven for drying and curing at 150 degrees Celsius.
[0041]Electroless copper plating is performed on the catalyzed original fabric, so that the surface of the original fabric fiber is plated with a conductive chemical copper layer. Wherein, the electroless copper plating liquid that adopts in the described electroless copper plating process mainly contains the copper chloride that concentration is 4.5 / L, the EDTA of 25g / L, the NaOH of 7g / L, the HCHO of 2g / L and a small amount of chemical copper stable agent, the plating temperature is controlled at 40-50 degrees Celsius. The chemical copper stab...
Embodiment 3
[0044] Embodiment 3 230T polyurethane fiber grid cloth
[0045] Using 230T polyurethane fiber grid cloth as the original cloth, the original cloth is dip-coated in the catalytic liquid mixed with palladium salt and PU resin solution at room temperature. The solid content of PU resin in the catalytic liquid is 1.0%, and the palladium content is 340ppm. After pressing, enter the oven for drying and curing at 180 degrees Celsius.
[0046] Electroless copper plating is performed on the catalyzed original fabric, so that the surface of the original fabric fiber is plated with a conductive chemical copper layer. Wherein, the electroless copper plating liquid that adopts in the described electroless copper plating process mainly contains the copper chloride that concentration is 6g / L, the EDTA of 28g / L, the NaOH of 8g / L, the HCHO of 3g / L and a small amount of chemical copper stable agent, the plating temperature is controlled at 40-50 degrees Celsius. The chemical copper stabilizer...
PUM
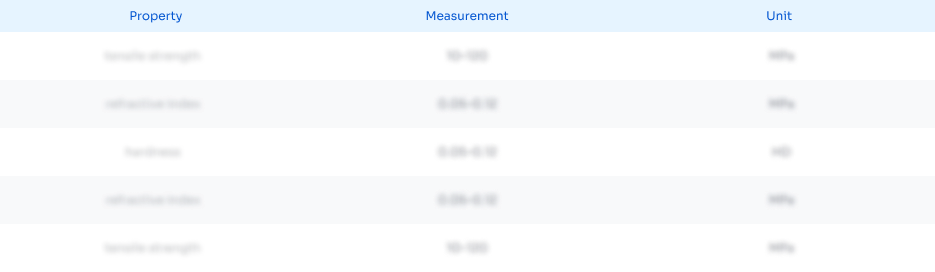
Abstract
Description
Claims
Application Information

- Generate Ideas
- Intellectual Property
- Life Sciences
- Materials
- Tech Scout
- Unparalleled Data Quality
- Higher Quality Content
- 60% Fewer Hallucinations
Browse by: Latest US Patents, China's latest patents, Technical Efficacy Thesaurus, Application Domain, Technology Topic, Popular Technical Reports.
© 2025 PatSnap. All rights reserved.Legal|Privacy policy|Modern Slavery Act Transparency Statement|Sitemap|About US| Contact US: help@patsnap.com