Wet-method phosphoric acid staged extraction and purification process
A wet-process phosphoric acid and purification process technology, applied in the fields of phosphorus compounds, inorganic chemistry, chemical instruments and methods, etc., can solve the problems of poor adaptability of wet-process phosphoric acid raw material diversity, difficult comprehensive cost of phosphorus resource conversion, etc. The effect of comprehensive purification rate and cost reduction
- Summary
- Abstract
- Description
- Claims
- Application Information
AI Technical Summary
Problems solved by technology
Method used
Examples
Embodiment 1
[0017] (1) At a temperature of 50°C, according to methyl isobutyl ketone and P 2 o 5 Concentration is 50wt% wet-process phosphoric acid mass ratio is the ratio extraction wet-process phosphoric acid of 8:1, obtains loaded methyl isobutyl ketone and primary raffinate after phase separation;
[0018] (2) At a temperature of 50°C, use a mixed solvent of tributyl phosphate and n-butanol at a volume ratio of 3:1 to extract the primary raffinate obtained in step (1), the mixed solvent and a The volume ratio of grade raffinate is 10:1;
[0019] (3) Methyl isobutyl ketone loaded with phosphoric acid further removes sulfate radical impurities by adding barium carbonate aqueous solution, and then further removes metal impurities through washing and back extraction with water, so as to obtain phosphoric acid aqueous solution; the obtained phosphoric acid aqueous solution is adsorbed Further remove impurities such as fluorine and arsenic, and then prepare food-grade phosphoric acid prod...
Embodiment 2
[0024] (1) At a temperature of 40°C, according to methyl isobutyl ketone and P 2 o 5 The mass ratio of wet-process phosphoric acid with a concentration of 55wt% is 6:1 to extract wet-process phosphoric acid, and obtain loaded methyl isobutyl ketone and primary raffinate after phase separation;
[0025] (2) At a temperature of 40°C, use a mixed solvent of tributyl phosphate and n-hexane with a volume ratio of 5:1 to extract the primary raffinate obtained in step (1), the mixed solvent and the primary The volume ratio of raffinate is 5:1;
[0026] (3) Methyl isobutyl ketone loaded with phosphoric acid further removes sulfate radical impurities by adding barium carbonate aqueous solution, and then further removes metal impurities through washing and back extraction with water, so as to obtain phosphoric acid aqueous solution; the obtained phosphoric acid aqueous solution is adsorbed Further remove impurities such as fluorine and arsenic, and then prepare food-grade phosphoric a...
Embodiment 3
[0031] (1) At a temperature of 30°C, according to methyl isobutyl ketone and P 2 o 5 Concentration is 60wt% wet-process phosphoric acid mass ratio is the ratio of 3:1 to extract wet-process phosphoric acid, obtain loaded methyl isobutyl ketone and primary raffinate after phase separation;
[0032] (2) At a temperature of 30°C, extract the primary raffinate obtained in step (1) with a mixed solvent of tributyl phosphate and cyclohexane with a volume ratio of 10:1, the mixed solvent and a The volume ratio of grade raffinate is 2:1;
[0033] (3) Methyl isobutyl ketone loaded with phosphoric acid further removes sulfate radical impurities by adding barium carbonate aqueous solution, and then further removes metal impurities through washing and back extraction with water, so as to obtain phosphoric acid aqueous solution; the obtained phosphoric acid aqueous solution is adsorbed Further remove impurities such as fluorine and arsenic, and then prepare food-grade phosphoric acid pro...
PUM
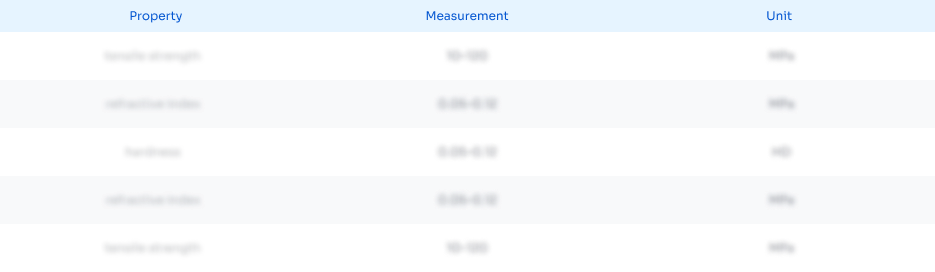
Abstract
Description
Claims
Application Information

- R&D
- Intellectual Property
- Life Sciences
- Materials
- Tech Scout
- Unparalleled Data Quality
- Higher Quality Content
- 60% Fewer Hallucinations
Browse by: Latest US Patents, China's latest patents, Technical Efficacy Thesaurus, Application Domain, Technology Topic, Popular Technical Reports.
© 2025 PatSnap. All rights reserved.Legal|Privacy policy|Modern Slavery Act Transparency Statement|Sitemap|About US| Contact US: help@patsnap.com