Method for computing accurate value of carbon equivalent of cast iron and application of method
A calculation method and carbon equivalent technology, applied in the field of cast iron alloys, can solve problems such as failure to consider the content and role of trace elements, inability to accurately control carbon equivalent, increase in shrinkage defects in castings, etc. Reducing the effect of internal shrinkage
- Summary
- Abstract
- Description
- Claims
- Application Information
AI Technical Summary
Problems solved by technology
Method used
Image
Examples
Embodiment 1
[0019] In the present embodiment, its method is as follows:
[0020] a) According to the furnace charge ratio: 30% pig iron, 18% scrap steel, 52% returned iron, the molten iron is smelted by an induction furnace, and the mass fraction of carbon in the molten iron is detected by a spectrometer w(C), and the mass fraction of silicon w(Si ), the mass fraction w(M) of each element except iron in molten iron i , w(M) involved in this example i Including w(C), w(Si), w(Mn), w(P), w(S), w(Cu), w(Sn), w(Cr), w(V) and w(Mo) , the test results are shown in Table 2;
[0021] b) Establish carbon equivalent formula Among them, q is the graphitization tendency index of elements, which is 0 for elements that promote graphitization, and 1 for elements that hinder graphitization; n is the number of elements, and k is the graphitization degree coefficient of elements in molten iron; q, n, The k value is shown in Table 1, and the q, n, k values and the mass fraction w(M) of each element m...
Embodiment 2
[0028] In the present embodiment, its method is as follows:
[0029] a) According to the furnace charge ratio: 40% pig iron, 18% scrap steel, 42% returned iron, the molten iron is smelted by an induction furnace, and the mass fraction of carbon in the molten iron is detected by a spectrometer w(C), and the mass fraction of silicon w(Si ), the mass fraction w(M) of each element except iron in molten iron i , w(M) involved in this example i Same as embodiment 1, the graphitization degree coefficient k of elements in the molten iron;
[0030] b) Establish carbon equivalent formula Among them, q is the graphitization tendency index of elements, which is 0 for elements that promote graphitization, and 1 for elements that hinder graphitization; n is the number of elements, and k is the graphitization degree coefficient of elements in molten iron; q, n, The k value is shown in Table 1, and the q, n, k values and the mass fraction w(M) of each element measured in step a) i Subs...
PUM
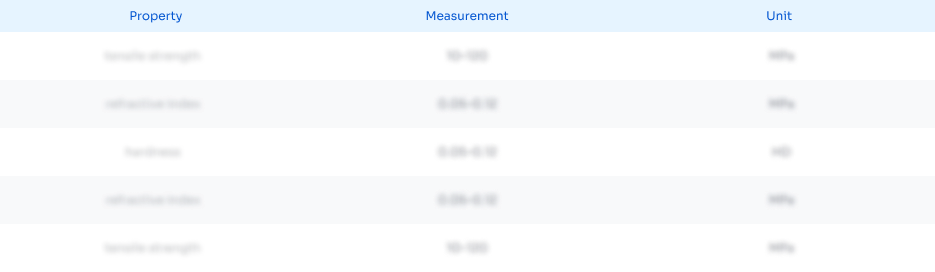
Abstract
Description
Claims
Application Information

- R&D
- Intellectual Property
- Life Sciences
- Materials
- Tech Scout
- Unparalleled Data Quality
- Higher Quality Content
- 60% Fewer Hallucinations
Browse by: Latest US Patents, China's latest patents, Technical Efficacy Thesaurus, Application Domain, Technology Topic, Popular Technical Reports.
© 2025 PatSnap. All rights reserved.Legal|Privacy policy|Modern Slavery Act Transparency Statement|Sitemap|About US| Contact US: help@patsnap.com