1, 2-dichloroethane cracking catalyst, as well as preparation method and application thereof
A technology for cracking catalysts and dichloroethane, applied in 1 field, can solve the problems of high reaction temperature, energy waste, cost increase, etc., and achieve the effect of low reaction temperature, high conversion rate of dichloroethane, and stable operation
- Summary
- Abstract
- Description
- Claims
- Application Information
AI Technical Summary
Problems solved by technology
Method used
Examples
Embodiment 1
[0016] [Example 1] 60 g of a catalyst with a loading capacity of 20% is filled in an experimental fixed-bed reactor, and the investigation on the reaction activity of 1,2-dichloroethane cracking to vinyl chloride is carried out at normal pressure and 320° C., wherein Mass space velocity of 0.8 hours -1 , The cracking rate of dichloroethane is 33.27%.
Embodiment 2
[0017] [Example 2] 60 g of a catalyst with a loading capacity of 20% is filled in an experimental fixed-bed reactor, and the investigation of the reaction activity of 1,2-dichloroethane cracking to vinyl chloride is carried out at normal pressure and 340° C., wherein Mass space velocity of 1.6 hours -1 , The cracking rate of dichloroethane is 48.59%.
Embodiment 3
[0018] [Example 3] 55 g of catalysts with a loading capacity of 10% were filled in an experimental fixed-bed reactor, and the investigation of the reaction activity of 1,2-dichloroethane cracking to vinyl chloride was carried out at normal pressure and 360° C., wherein Mass space velocity of 0.90 hours -1 , The cracking rate of dichloroethane is 99.23%.
PUM
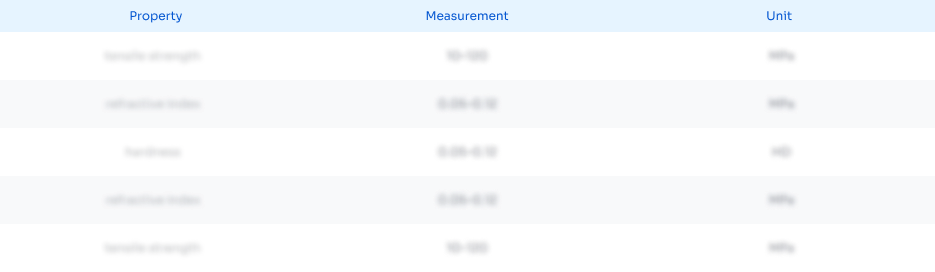
Abstract
Description
Claims
Application Information

- R&D
- Intellectual Property
- Life Sciences
- Materials
- Tech Scout
- Unparalleled Data Quality
- Higher Quality Content
- 60% Fewer Hallucinations
Browse by: Latest US Patents, China's latest patents, Technical Efficacy Thesaurus, Application Domain, Technology Topic, Popular Technical Reports.
© 2025 PatSnap. All rights reserved.Legal|Privacy policy|Modern Slavery Act Transparency Statement|Sitemap|About US| Contact US: help@patsnap.com