Method for preparing high-seepage-resistance calcium sulfoaluminate concrete
A technology of sulphoaluminate and sulphoaluminate cement, which is applied in the field of concrete materials, can solve problems such as poor durability, easy aging, and easy combustion, and achieve excellent impermeability and erosion resistance, simple preparation method, and improved effect of density
- Summary
- Abstract
- Description
- Claims
- Application Information
AI Technical Summary
Problems solved by technology
Method used
Examples
Embodiment 1
[0021] The aggregate particle size and the corresponding parts by weight of the aggregate are as follows:
[0022] Fine aggregate particle size parts by weight Coarse aggregate particle size parts by weight 0.075~0.15mm 2.56 2.36~4.75mm 17.36 0.15~0.3mm 3.75 4.75~9.5mm 25.05 0.3~0.6mm 5.72 9.50~16mm 26.04 0.6~1.18mm 7.89 1.18~2.36mm 11.64
[0023] Raw materials and parts by weight of high impermeability concrete:
[0024] Sulphoaluminate cement 18.12
[0025] Aggregate 75.16
[0026] water 6.34
[0027] Polycarboxylic acid 0.36
[0028] Boric acid 0.02
[0029] Concrete molding process, weighing raw materials according to the concrete mix ratio, the mixing method adopts a three-step mixing process: first add 18.12 parts of sulphoaluminate cement, 0.02 parts of boric acid and 3.17 parts of water and stir for 30 seconds, then add 75.16 parts of aggregate The material was stirred for 60s, and finally ...
Embodiment 2
[0032] The aggregate particle size and the corresponding parts by weight of the aggregate are as follows:
[0033] Fine aggregate particle size parts by weight Coarse aggregate particle size parts by weight 0.075~0.15mm 3.52 2.36~4.75mm 17.49 0.15~0.3mm 5.00 4.75~9.5mm 23.31 0.3~0.6mm 6.94 9.50~16mm 22.61 0.6~1.18mm 8.95 1.18~2.36mm 12.18
[0034] The parts by weight of each raw material and its components in the concrete are:
[0035] Sulphoaluminate cement 21.55
[0036] Aggregate 71.75
[0037] water 6.45
[0038] Polycarboxylate 0.22
[0039] Boric acid 0.03
[0040] Concrete molding process, weighing raw materials according to the mix ratio, the mixing method adopts a three-step mixing process: first add 21.55 parts of sulphoaluminate cement, 0.03 parts of boric acid and 3.23 parts of water and stir for 35 seconds, then add 71.75 parts of aggregate and stir 70s, finally add 0.22 parts of ...
Embodiment 3
[0043] The aggregate particle size and the corresponding parts by weight of the aggregate are as follows:
[0044] Fine aggregate particle size parts by weight Coarse aggregate particle size parts by weight 0.075~0.15mm 5.37 2.36~4.75mm 19.42 0.15~0.3mm 7.02 4.75~9.5mm 17.77 0.3~0.6mm 8.68 9.50~16mm 16.12 0.6~1.18mm 11.16 1.18~2.36mm 14.46
[0045] The parts by weight of each raw material and its components in the concrete are:
[0046] Sulphoaluminate cement 27.00
[0047] Aggregate 65.91
[0048] water 6.75
[0049] Polycarboxylate 0.30
[0050] Boric acid 0.04
[0051] Concrete molding process, weighing raw materials according to the mixing ratio, the mixing method adopts a three-step mixing process: first add 27.00 parts of sulphoaluminate cement, 0.04 parts of boric acid and 3.38 parts of water and stir for 25 seconds, then add 65.91 parts of aggregate and stir 60s, finally add 0.30 parts...
PUM
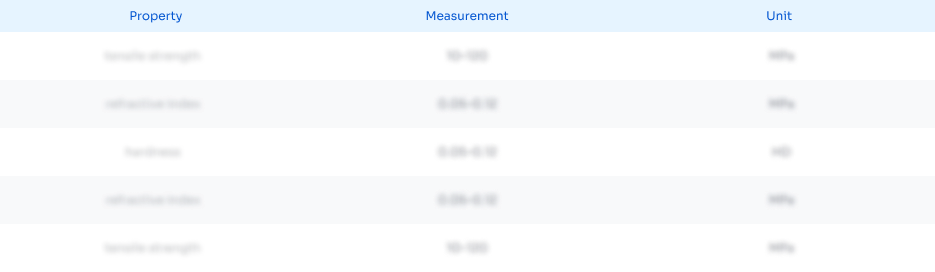
Abstract
Description
Claims
Application Information

- R&D
- Intellectual Property
- Life Sciences
- Materials
- Tech Scout
- Unparalleled Data Quality
- Higher Quality Content
- 60% Fewer Hallucinations
Browse by: Latest US Patents, China's latest patents, Technical Efficacy Thesaurus, Application Domain, Technology Topic, Popular Technical Reports.
© 2025 PatSnap. All rights reserved.Legal|Privacy policy|Modern Slavery Act Transparency Statement|Sitemap|About US| Contact US: help@patsnap.com