Method for preparing cerium-containing zinc coating
A technology of zinc coating and plating solution, which is applied in the field of preparation of cerium-containing zinc coating, can solve problems such as difficult preparation of rare earth, and achieve the effect of easy maintenance of plating solution and high current efficiency
- Summary
- Abstract
- Description
- Claims
- Application Information
AI Technical Summary
Problems solved by technology
Method used
Image
Examples
Embodiment 1
[0021] The preparation process and steps in this embodiment are as follows:
[0022] a. First prepare the sulfate solution of the ion to be plated, and dissolve 60g of crystalline zinc sulfate and 2g of cerous sulfate in distilled water to prepare a 1L plating solution.
[0023] b. Then add 20g of sodium citrate and 20g of sodium hypophosphite to dissolve completely; add dilute sulfuric acid to adjust the pH value to 2, and control the temperature of the plating solution to 55°C.
[0024] c. Electrodeposition is carried out by DC electroplating method; in the electroplating tank filled with the above-mentioned sulfate plating solution, the steel plate to be plated is used as the cathode, and the platinum sheet is used as the anode, and 0.6A / cm 2 The DC current was electroplated for 2 minutes; the Ce content in the coating was finally measured by AES to be 0.1wt%.
Embodiment 2
[0026] The preparation process and steps in this embodiment are as follows:
[0027] a. First prepare the sulfate solution of the ions to be plated. Dissolve 100g of crystalline zinc sulfate and 2g of cerous sulfate in distilled water to prepare a 1L plating solution.
[0028] b. Then add 20g of sodium citrate and 20g of sodium hypophosphite to dissolve completely; add dilute sulfuric acid to adjust the pH value to 2, and control the temperature of the plating solution to 55°C.
[0029] c. Electrodeposition is carried out by DC electroplating method; in the electroplating tank filled with the above-mentioned sulfate plating solution, the steel plate to be plated is used as the cathode, and the platinum sheet is used as the anode, and 1A / cm 2 The DC current was used for electroplating for 2 minutes; the Ce content in the coating was finally measured by AES to be 0.065wt%.
Embodiment 3
[0031] The preparation process and steps in this embodiment are as follows:
[0032] a. First prepare the sulfate solution of the ions to be plated. Dissolve 350g of crystalline zinc sulfate and 2g of cerous sulfate in distilled water to prepare a 1L plating solution.
[0033] b. Then add 30g of sodium citrate and 30g of sodium hypophosphite to dissolve completely; add dilute sulfuric acid to adjust the pH value to 2, and control the temperature of the plating solution to 25°C.
[0034] c. Electrodeposition is carried out by DC electroplating method; in the electroplating tank filled with the above-mentioned sulfate plating solution, the steel plate to be plated is used as the cathode, and the platinum sheet is used as the anode, and 2A / cm 2 The DC current was electroplated for 2 minutes; the Ce content in the coating was finally measured by AES to be 0.05wt%.
PUM
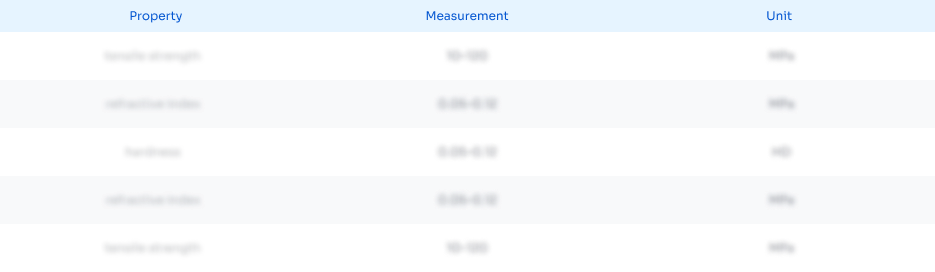
Abstract
Description
Claims
Application Information

- Generate Ideas
- Intellectual Property
- Life Sciences
- Materials
- Tech Scout
- Unparalleled Data Quality
- Higher Quality Content
- 60% Fewer Hallucinations
Browse by: Latest US Patents, China's latest patents, Technical Efficacy Thesaurus, Application Domain, Technology Topic, Popular Technical Reports.
© 2025 PatSnap. All rights reserved.Legal|Privacy policy|Modern Slavery Act Transparency Statement|Sitemap|About US| Contact US: help@patsnap.com