Method for producing solid poly ferric sulfate
A technology of solid polymerization and ferric sulfate, which is applied in the fields of ferric sulfate, flocculation/precipitation water/sewage treatment, etc. It can solve the problems of low basicity of products, poor flocculation effect, complicated process conditions, etc., and achieve simple operation process and high production efficiency. Inexpensive and versatile effects
- Summary
- Abstract
- Description
- Claims
- Application Information
AI Technical Summary
Problems solved by technology
Method used
Examples
Embodiment 1
[0010] Weigh 800 Kg industrial ferrous sulfate (FeSO 4 ·7H 2 O), put it into an acid-resistant reaction kettle, and heat it to 80±5 o C, electric stirring until muddy, then spray 80 Kg of concentrated sulfuric acid with a mass concentration of 98% and 160 Kg of hydrogen peroxide with a mass concentration of 50% in the reaction kettle, fully stir the reaction for 1 hour after adding, add industrial grade ammonium salt amino Sodium 1 Kg, ammonium bicarbonate 2 Kg and ammonium chloride 13 Kg, after stirring evenly, the product is all moved to a condensation tank, cooled, and left to stand for 8 hours to obtain powdery solid polyferric sulfate.
Embodiment 2
[0012] Weigh 800 Kg industrial ferrous sulfate (FeSO 4 ·7H 2 O), put it into an acid-resistant reactor and heat it to 130±5 o C, electric stirring until muddy, then spraying 104 Kg of concentrated sulfuric acid with a mass concentration of 98% and 240 Kg of hydrogen peroxide with a mass concentration of 50% in the reaction kettle, fully stirred and reacted for 4 hours after the addition, and added industrial-grade ammonium salt amino Sodium 3 Kg, ammonium bicarbonate 8 Kg and ammonium chloride 37 Kg, after stirring evenly, the product is all moved to a condensation tank, cooled, and left to stand for 36 hours to obtain powdery solid polyferric sulfate.
Embodiment 3
[0014] Weigh 800 Kg industrial ferrous sulfate (FeSO 4 ·7H 2 O), put it into an acid-resistant reaction kettle, and heat it to 100±5 o C, electric stirring until muddy, and then spraying 95 Kg of concentrated sulfuric acid with a mass concentration of 98% and 200 Kg of hydrogen peroxide with a mass concentration of 50% in the reaction kettle, fully stirred and reacted for 2 hours after the addition, and added industrial-grade ammonium salt amino Sodium 1 Kg, ammonium bicarbonate 8 Kg and ammonium chloride 14 Kg, after stirring evenly, the product is all moved to a condensation tank, cooled, and left to stand for 12 hours to obtain powdery solid polyferric sulfate.
PUM
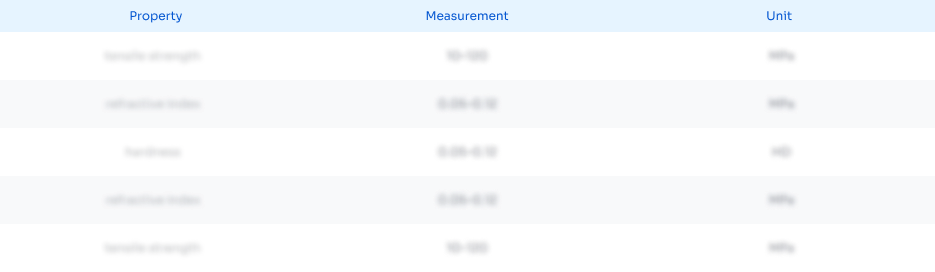
Abstract
Description
Claims
Application Information

- R&D Engineer
- R&D Manager
- IP Professional
- Industry Leading Data Capabilities
- Powerful AI technology
- Patent DNA Extraction
Browse by: Latest US Patents, China's latest patents, Technical Efficacy Thesaurus, Application Domain, Technology Topic, Popular Technical Reports.
© 2024 PatSnap. All rights reserved.Legal|Privacy policy|Modern Slavery Act Transparency Statement|Sitemap|About US| Contact US: help@patsnap.com