Environment-friendly vapor phase rust-proof film
A gas-phase anti-rust and film technology, applied in the field of film required for metal product packaging, can solve the problems of harming human beings, pollute the environment, poor anti-rust performance, etc., and achieve the effects of low cost, no environmental pollution, and good anti-rust performance.
- Summary
- Abstract
- Description
- Claims
- Application Information
AI Technical Summary
Problems solved by technology
Method used
Image
Examples
Embodiment 1
[0020] First, weigh 1kg of gas phase corrosion inhibitor (VCI) raw material sodium benzoate, 1kg of tungstate, 2kg of diamine type containing morpholine unit, 0.3kg of dispersed lubricant raw material, 2.5kg of carrier plastic raw material, and mix the components After uniformity, put it into a high-speed mixer and mix for 30 minutes. The friction heat generated by the high-speed mixer will make the carrier plastic raw material particles sticky, and the dispersed lubricant raw material will be melted under the action of shear heat. When the VCI evenly adheres to the carrier plastic The raw materials are discharged when they are loaded, and after natural cooling, they are put into the granulator for granulation to obtain the prepared additive granules. Then, according to the ratio of three to one, weigh 60kg of base plastic raw materials LDPE and 20kg of LLDPE, mix them evenly with the prepared additive particles, and put them into the extrusion barrel of the blow molding machin...
Embodiment 2
[0022] First, weigh 2kg of gas phase corrosion inhibitor (VCI) raw material sodium benzoate, 1kg of tungstate, 1.5kg of diamine type containing morpholine unit, 0.2kg of dispersed lubricant raw material, 2.0kg of carrier plastic raw material, and mix each component After mixing evenly, put it into a high-speed mixer and mix for 30 minutes. The friction heat generated by the high-speed mixer will make the carrier plastic raw material particles sticky, and the dispersed lubricant raw materials will be melted under the action of shear heat. When the VCI is evenly adhered to the carrier The plastic raw materials are discharged when they are put on, and after natural cooling, they are put into the granulator for granulation to obtain the prepared additive granules. Then, according to the ratio of one to one, weigh 40kg of base plastic raw materials LDPE and 40kg of LLDPE, mix them evenly with the prepared additive particles, and put them into the extrusion barrel of the blow molding...
Embodiment 3
[0024] First, weigh 1.5kg of gas-phase corrosion inhibitor (VCI) raw material sodium benzoate, 1.5kg of tungstate, 1.5kg of diamine type containing morpholine unit, 0.3kg of dispersed lubricant raw material, and 1.5kg of carrier plastic raw material. After the components are mixed evenly, put them into a high-speed mixer and mix for 30 minutes. The friction heat generated by the high-speed mixer will make the carrier plastic raw material particles sticky, and the dispersed lubricant raw materials will be melted under the action of shear heat. When the VCI is uniformly adhered The material is discharged when it is on the carrier plastic raw material, and after natural cooling, it is put into the granulator for granulation to obtain the prepared additive granules. Then, according to the ratio of three to one, weigh 45 kg of base plastic raw materials LDPE and 15 kg of LLDPE, mix them evenly with the prepared additive particles, and put them into the extrusion barrel of the blow m...
PUM
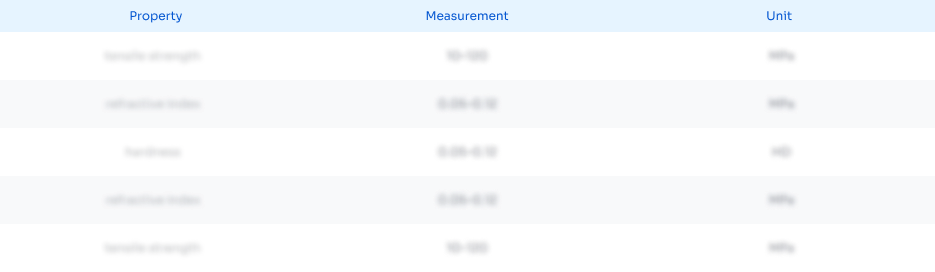
Abstract
Description
Claims
Application Information

- R&D
- Intellectual Property
- Life Sciences
- Materials
- Tech Scout
- Unparalleled Data Quality
- Higher Quality Content
- 60% Fewer Hallucinations
Browse by: Latest US Patents, China's latest patents, Technical Efficacy Thesaurus, Application Domain, Technology Topic, Popular Technical Reports.
© 2025 PatSnap. All rights reserved.Legal|Privacy policy|Modern Slavery Act Transparency Statement|Sitemap|About US| Contact US: help@patsnap.com