Catalyst for preparing vinyl fluoride and 1,1-difluoroethane by using acetylene fluoride and preparation method for catalyst
A technology of fluorinated acetylene and difluoroethane, which is applied in the field of chemical catalysts and their preparation, can solve problems such as carbon deposition, impact on catalyst performance, and impact on catalyst life, and achieve good activity and selectivity.
- Summary
- Abstract
- Description
- Claims
- Application Information
AI Technical Summary
Problems solved by technology
Method used
Image
Examples
Embodiment 1
[0023] ①According to Cr, the molar ratio of La is 0.1:1, Cr 2 o 3 and La 2 o 3 The mass percentage is 1%, weigh Cr(NO 3 ) 3 9H 2 O and La(NO 3 ) 3 ·6H 2 O, add an appropriate amount of distilled water to prepare a solution, and press γ-Al 2 o 3 The mass percentage is 99%, the γ-Al 2 o 3 Add to the above solution, stir evenly, and immerse at room temperature for 4 hours;
[0024] ②Finally, dry in an oven at 120°C for 12 hours, and then bake in an air atmosphere at 1100°C for 4 hours to obtain a powder;
[0025] ③ The obtained powder was pretreated by anhydrous HF at 450°C for 4 hours, and then passed through N 2 Until being cooled to room temperature to obtain the catalyst Cr of the present invention 2 o 3 -La 2 o 3 / AlF 3 -α-Al 2 o 3 . After the reaction, γ-Al 2 o 3 Converted to β-AlF after high temperature calcination and fluorination 3 , α-AlF 3 , α-Al 2 o 3 mixture. β-AlF 3 , α-AlF 3 , α-Al 2 o 3 The total molar amount of γ-Al is equal to 2 ...
Embodiment 2
[0028] ①According to Cr, the molar ratio of La is 0.5:1, Cr 2 o 3 and La 2 o 3 The mass percentage is 2%, weigh Cr(NO 3 ) 3 9H 2 O and La(NO 3 ) 3 ·6H 2 O, add an appropriate amount of distilled water to prepare a solution, and press γ-Al 2 o 3 The mass percentage is 98% will γ-Al 2 o 3 Add to the above solution, stir evenly, and immerse at room temperature for 4 hours;
[0029] ②Finally, dry in an oven at 120°C for 12 hours, and then bake in an air atmosphere at 1100°C for 4 hours to obtain a powder;
[0030] ③ The obtained powder was pretreated by anhydrous HF at 450°C for 5 hours, and then passed through N 2 Until being cooled to room temperature to obtain the catalyst Cr of the present invention 2 o 3 -La 2 o 3 / AlF 3 -α-Al 2 o 3 . After the reaction, γ-Al 2 o 3 Converted to β-AlF after high temperature roasting and fluorination 3 , α-AlF 3 , α-Al 2 o 3 mixture. β-AlF 3 , α-AlF 3 , α-Al 2 o 3 The total molar amount of γ-Al is equal to 2 o ...
Embodiment 3
[0033] ①According to Cr, the molar ratio of La is 1:1, Cr 2 o 3 and La 2 o 3 The mass percentage is 5%, weigh Cr(NO 3 ) 3 9H 2 O and La(NO 3 ) 3 ·6H 2 O, add an appropriate amount of distilled water to prepare a solution, and press γ-Al 2 o 3 The mass percentage is 95% will γ-Al 2 o 3 Add to the above solution, stir evenly, and immerse at room temperature for 4 hours;
[0034] ②Finally, dry in an oven at 120°C for 12 hours, and then bake in an air atmosphere at 1100°C for 4 hours to obtain a powder;
[0035] ③ The obtained powder was pretreated by anhydrous HF at 450°C for 6 hours, and then passed through N 2 Until being cooled to room temperature to obtain the catalyst Cr of the present invention 2 o 3 -La 2 o 3 / AlF 3 -α-Al 2 o 3 . After the reaction, γ-Al 2 o 3 Converted to β-AlF after high temperature roasting and fluorination 3 , α-AlF 3 , α-Al 2 o 3 mixture. β-AlF 3 , α-AlF 3 , α-Al 2 o 3 The total molar amount of γ-Al is equal to 2 o 3 ...
PUM
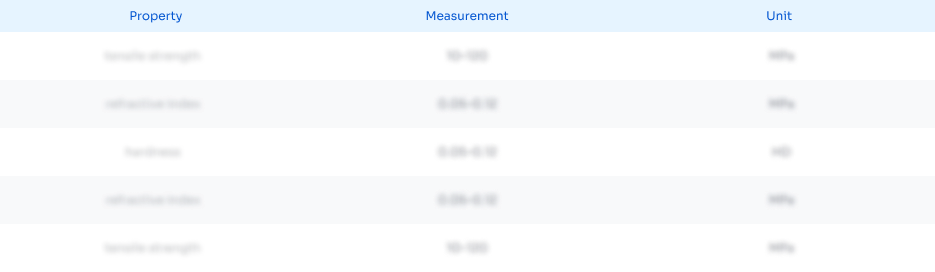
Abstract
Description
Claims
Application Information

- R&D Engineer
- R&D Manager
- IP Professional
- Industry Leading Data Capabilities
- Powerful AI technology
- Patent DNA Extraction
Browse by: Latest US Patents, China's latest patents, Technical Efficacy Thesaurus, Application Domain, Technology Topic, Popular Technical Reports.
© 2024 PatSnap. All rights reserved.Legal|Privacy policy|Modern Slavery Act Transparency Statement|Sitemap|About US| Contact US: help@patsnap.com