Granulator with ring mould
A granulator and ring die technology, which is applied in the direction of mold extrusion granulation, presses, manufacturing tools, etc., can solve problems such as easy failure, high probability of support shaft breakage, and difficult maintenance
- Summary
- Abstract
- Description
- Claims
- Application Information
AI Technical Summary
Problems solved by technology
Method used
Image
Examples
Embodiment Construction
[0015] The specific technical solution of the ring die granulator of the present invention will be further described below in conjunction with the accompanying drawings and preferred embodiments.
[0016] refer to Figure 1 to Figure 4 . A ring die granulator includes a machine base 1, a drive motor 2, a reducer 3, a ring die base 4 is installed on the output shaft of the reducer 3, the ring die base 4 is closely connected with a ring die 5, and the pressure roller assembly 6 is located on the In the ring die 5 , a pressing chamber 7 is formed with the ring die 5 , and the pressing roller assembly 6 includes a left pressing roller assembly 60 and a right pressing roller assembly 61 arranged symmetrically. The structure of the left pressing roller assembly 60 is the same as that of the right pressing roller assembly 61 , and the left pressing roller assembly 60 is taken as an example for illustration. The left pressure roller 62 of the left pressure roller assembly 60 is fixe...
PUM
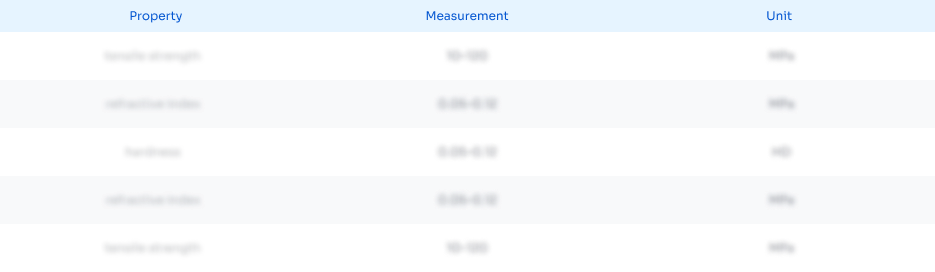
Abstract
Description
Claims
Application Information

- Generate Ideas
- Intellectual Property
- Life Sciences
- Materials
- Tech Scout
- Unparalleled Data Quality
- Higher Quality Content
- 60% Fewer Hallucinations
Browse by: Latest US Patents, China's latest patents, Technical Efficacy Thesaurus, Application Domain, Technology Topic, Popular Technical Reports.
© 2025 PatSnap. All rights reserved.Legal|Privacy policy|Modern Slavery Act Transparency Statement|Sitemap|About US| Contact US: help@patsnap.com