Method and system for feedback control simulation in heat treated (TRT) blast furnace top pressure control stamping process
A technology of feedback control and simulation method, which is applied to blast furnaces, blast furnace details, furnaces, etc., can solve the problems of top pressure fluctuation maintenance, blast furnace normal influence, disturbance, etc., and achieve the effect of convenient modeling
- Summary
- Abstract
- Description
- Claims
- Application Information
AI Technical Summary
Problems solved by technology
Method used
Image
Examples
Embodiment Construction
[0059] figure 2It is the top pressure control model diagram of TRT blast furnace, that is, the topological structure of the entire TRT simplified model. Boundary A produces a stable gas flow, which enters the blast furnace through pipe A, and the gas flows out of the furnace top through the material layer in the blast furnace, and passes through a long pipe B flows into the stator vane in the turbine, and finally flows out to the boundary B; there is a branch pipeline connected to the stamping tank in front of the stator vane, and a stamping valve is installed on the pipeline between the vane and the stamping tank, because the stamping valve is opened and closed. The blast furnace gas flow rate has a great influence, so the furnace top pressure will fluctuate with the opening and closing of the ram valve and the time when the ram valve is opened. This system and method is to simulate the impact of the switch of the stamping valve on the top pressure of the blast furnace. By t...
PUM
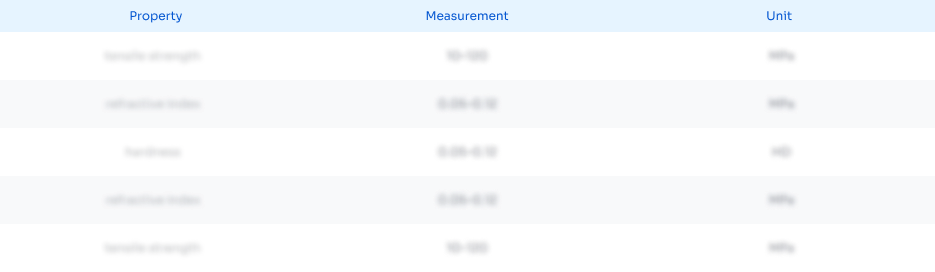
Abstract
Description
Claims
Application Information

- R&D
- Intellectual Property
- Life Sciences
- Materials
- Tech Scout
- Unparalleled Data Quality
- Higher Quality Content
- 60% Fewer Hallucinations
Browse by: Latest US Patents, China's latest patents, Technical Efficacy Thesaurus, Application Domain, Technology Topic, Popular Technical Reports.
© 2025 PatSnap. All rights reserved.Legal|Privacy policy|Modern Slavery Act Transparency Statement|Sitemap|About US| Contact US: help@patsnap.com