Method for preparing high thermal conductivity chopped carbon fiber reinforced polymer-based resistance welding unit
A chopped carbon fiber and resistance welding technology, which is applied in the field of preparation of high thermal conductivity chopped carbon fiber reinforced polymer-based resistance welding unit, can solve the problems of overshoot, uneven heating, overheating, etc., and achieve simple preparation process and improved thermal conductivity , the effect of expanding the scope of application
- Summary
- Abstract
- Description
- Claims
- Application Information
AI Technical Summary
Problems solved by technology
Method used
Examples
Embodiment 1
[0017] Ultrasonic dispersion of 10g of graphene microflakes and 2g of chopped carbon fibers with a length of 6mm for 4h, suction filtration, drying, then adding 1g of stearic acid and stirring evenly, mixed with 39g of polypropylene (PP) matrix in an internal mixer at 170 o C. Mixing for 10 minutes under the condition of 40r / min, using a mold with a size of 1.4mm×5mm×20mm, at 190 o C. Press the tablet for 8 minutes under the condition of 12MPa, and then put the pressed tablet in a 1mm×5mm×25mm mold, leave a gap of 2.5mm in length between the two ends of the sheet and the mold end, and add 6mm in the gap between the two ends. Chopped carbon fiber, at 190 o C. Press the tablet under the condition of 12MPa for 5 minutes. After the workpiece is cooled, grind it with sandpaper until the chopped carbon fibers at both ends are exposed to obtain a welded unit. The resistance value of this welding unit is 10 2 Order of magnitude, the thermal conductivity is 5 times that of polypropyl...
Embodiment 2
[0019] 5g of graphene microflakes and 5g of chopped carbon fibers with a length of 3mm were ultrasonically dispersed for 8h, filtered with suction, dried, then added with 0.5g of stearic acid and stirred evenly on the surface, and mixed with 42g of polyethylene matrix in an internal mixer at 180 o C. Mixing for 10 minutes under the condition of 40r / min, using a mold with a size of 1.4mm×5mm×20mm, at 180 o C. Press the tablet under the condition of 12MPa for 8 minutes, and then put the pressed tablet in a 1mm×5mm×25mm mold. Leave a gap of 2.5mm between the two ends of the sheet and the mold end, and add 5mm in the gap between the two ends. polycrystalline iron fiber, at 180 o C. Press the tablet under the condition of 12MPa for 5 minutes. After the workpiece is cooled, grind it with sandpaper until the polycrystalline iron fiber is exposed to obtain a welded unit. The resistance value of this welding unit is 10 2 Order of magnitude, the thermal conductivity is 4 times that of...
Embodiment 3
[0021] 15g of graphene microflakes and 5g of chopped carbon fibers with a length of 6mm were ultrasonically dispersed for 8h, filtered with suction, dried, then added with 0.5g of sodium dodecylsulfonate and stirred evenly, and mixed with 29g of ethylene-vinyl acetate copolymer matrix 80 in the refining machine o C. Mixing for 10 minutes under the condition of 40r / min, using a mold with a size of 1.4mm×5mm×20mm, at 80 o C. Press the tablet under the condition of 12MPa for 8 minutes, and then put the pressed sheet in a 1mm×5mm×25mm mold, leave a gap of 2.5mm between the two ends of the sheet and the mold end, and add carbon nanotubes to the gap at both ends, at 80 o C. Press the tablet under the condition of 12MPa for 5 minutes. After the workpiece is cooled, grind it with sandpaper until the carbon nanotubes are exposed to obtain a welded unit. The resistance value of this welding unit is 10 1 Order of magnitude, the thermal conductivity is 8 times that of the ethylene-viny...
PUM
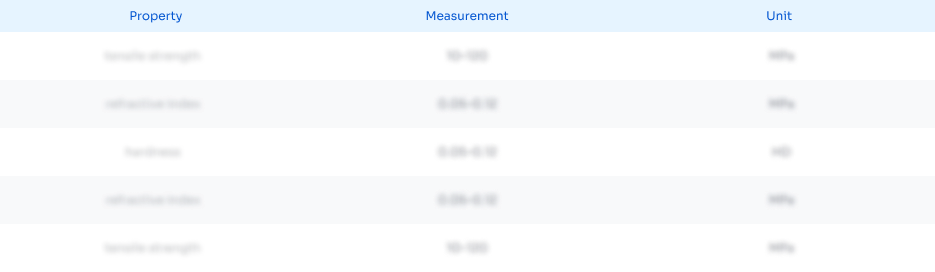
Abstract
Description
Claims
Application Information

- R&D Engineer
- R&D Manager
- IP Professional
- Industry Leading Data Capabilities
- Powerful AI technology
- Patent DNA Extraction
Browse by: Latest US Patents, China's latest patents, Technical Efficacy Thesaurus, Application Domain, Technology Topic, Popular Technical Reports.
© 2024 PatSnap. All rights reserved.Legal|Privacy policy|Modern Slavery Act Transparency Statement|Sitemap|About US| Contact US: help@patsnap.com