Method for recovering sulfur from atmospheric-pressure oxygen-rich leached residues of lead-zinc ores
An oxygen-enriched leaching, lead-zinc ore technology, applied in the field of resources and environment, can solve the problem of low sulfur purity, achieve the effects of high recovery rate and product quality, good environment and economic benefits, and simple process and equipment
- Summary
- Abstract
- Description
- Claims
- Application Information
AI Technical Summary
Problems solved by technology
Method used
Image
Examples
Embodiment 1
[0024] Take 3g of the oxygen-enriched leaching slag sample of zinc concentrate at atmospheric pressure with a sulfur content of 58.00% and a particle size below 100 mesh after drying, grinding, and screening, and put it into a horizontal vacuum distillation device, seal it, and evacuate it to 3000Pa About, heat to 200°C, keep the temperature constant, the sulfur vapor is extracted and condensed after the distillation device, after 30 minutes of distillation, cool down the reaction system to below 100°C, feed nitrogen into the distillation device, open the distillation device, and obtain Sulfur and metal residues. After calculation, the recovery rate of sulfur can reach 92.35%, and the product purity is 97.80%. The XRD patterns before and after distillation are as follows: figure 1 It can be seen from the figure that almost all the elemental sulfur in the slag after treatment is distilled out.
Embodiment 2
[0026] Take 10g of zinc concentrate atmospheric pressure oxygen-enriched leaching slag samples with a sulfur content of 18.60% and a particle size below 100 mesh after drying, grinding, and sieving, and put them into a horizontal vacuum distillation device, seal, and evacuate to 600Pa About, heat to 400°C, keep the temperature constant, the sulfur vapor is extracted and condensed after the distillation device, after 30 minutes of distillation, cool down the reaction system to below 100°C, feed nitrogen into the distillation device, open the distillation device, and obtain Sulfur and metal residues. After calculation, the recovery rate of sulfur can reach 91.04%, and the product purity is 95.12%.
Embodiment 3
[0028] Put 1 ton of zinc concentrate atmospheric pressure oxygen-enriched leaching slag with a sulfur content of 58.00% and a particle size below 100 mesh after drying, grinding, and screening into a horizontal continuous sulfur slag vacuum distillation industrial furnace, and vacuumize to 10,000Pa Around, heating to 300°C, keeping the temperature constant, the sulfur vapor is drawn out and condensed after the distillation device, after 120 minutes of distillation, the metal residue is discharged, re-feeding, and the next round of distillation process starts. The obtained sulfur and metal residues are collected, weighed and calculated to obtain a sulfur recovery rate of 90.57% and a product purity of 95.80%. Each cycle consumes about 400-1000 degrees of electricity, and no waste water, waste gas and other pollutants are produced.
PUM
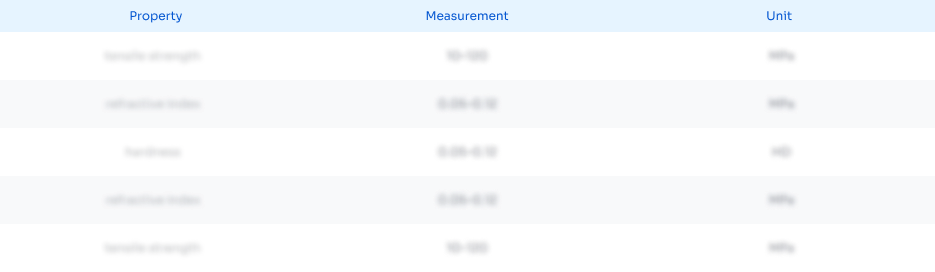
Abstract
Description
Claims
Application Information

- R&D
- Intellectual Property
- Life Sciences
- Materials
- Tech Scout
- Unparalleled Data Quality
- Higher Quality Content
- 60% Fewer Hallucinations
Browse by: Latest US Patents, China's latest patents, Technical Efficacy Thesaurus, Application Domain, Technology Topic, Popular Technical Reports.
© 2025 PatSnap. All rights reserved.Legal|Privacy policy|Modern Slavery Act Transparency Statement|Sitemap|About US| Contact US: help@patsnap.com