Reactive dye-white discharge printing paste and preparation method thereof
A technology for reactive dyes and printing paste, which is applied in dyeing, textile and papermaking, etc., can solve the problems of poor resistance to whitening agents, not enough environmental protection, and hindering the popularization and application of reactive dyes for whitening printing.
- Summary
- Abstract
- Description
- Claims
- Application Information
AI Technical Summary
Problems solved by technology
Method used
Image
Examples
Embodiment 1
[0024] (1) Take 190 grams of water, 75 grams of acrylic acid, 9 grams of acrylamide, and 57 grams of methacrylic acid, neutralize with 362 grams of ammonia water with a mass percentage concentration of 20-22%, and obtain a neutralization solution, which is pumped into No. 1 high-level tank and waits Use; 78 grams of 2-acrylamido-2-methylpropanesulfonic acid is pumped into No. 2 high-level tank for use;
[0025] (2) Add 174 grams of water to the reaction kettle, heat up to 73°C, add 0.7 grams of ammonium persulfate and 8 grams of water to prepare an ammonium persulfate aqueous solution, and heat up while stirring, when the temperature in the reaction kettle rises to 75-76°C At this time, start to add the neutralizing solution and 2-acrylamido-2-methylpropanesulfonic acid dropwise at the same time, keep the temperature at 76-78°C, finish adding in 3 hours to 4 hours, and start dropping 30 minutes before the end of the dropwise addition Add ammonium persulfate aqueous solution pr...
Embodiment 2
[0030] (1) Take 194 grams of water, 77 grams of acrylic acid, 9.5 grams of acrylamide, and 58 grams of methacrylic acid, and neutralize with 365 grams of ammonia water with a concentration of 20%-22% in mass percentage to obtain a neutralization solution, which is pumped into No. 1 high-level The tank is ready for use; 79 grams of 2-acrylamide-2-methylpropanesulfonic acid is pumped into the No. 2 high-level tank for use;
[0031] (2) Add 177 grams of water to the reaction kettle, raise the temperature to 73°C, and add an aqueous ammonium persulfate solution prepared by adding 0.74 grams of ammonium persulfate and 8 grams of water. Raise the temperature while stirring, when the temperature in the reactor rises to 75-76°C, start to drop the materials in the No. 1 high-level tank and No. Finish. 30 minutes before the end of the dropwise addition, start to drop the ammonium persulfate aqueous solution prepared by 0.6 grams of ammonium persulfate and 4 grams of water, and finish a...
Embodiment 3
[0036] (1) Take 197 grams of water, 79 grams of acrylic acid, 10.5 grams of acrylamide, and 60 grams of methacrylic acid, and neutralize with 370 grams of ammonia water with a concentration of 20%-22% in mass percentage to obtain a neutralization solution, which is pumped into No. 1 high-level The tank is ready for use; 81 grams of 2-acrylamide-2-methylpropanesulfonic acid is pumped into the No. 2 high-level tank for use;
[0037] (2) Add 180 grams of water to the reaction kettle, raise the temperature to 73°C, and add an aqueous ammonium persulfate solution prepared by adding 0.78 grams of ammonium persulfate and 9 grams of water. Raise the temperature while stirring, when the temperature in the reactor rises to 75-76°C, start to drop the materials in the No. 1 high-level tank and No. Finish. 30 minutes before the end of the dropwise addition, start to drop the ammonium persulfate aqueous solution prepared by 0.65 grams of ammonium persulfate and 5 grams of water, and finish...
PUM
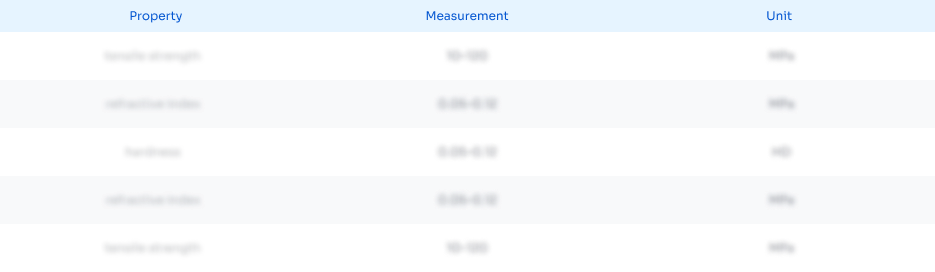
Abstract
Description
Claims
Application Information

- R&D
- Intellectual Property
- Life Sciences
- Materials
- Tech Scout
- Unparalleled Data Quality
- Higher Quality Content
- 60% Fewer Hallucinations
Browse by: Latest US Patents, China's latest patents, Technical Efficacy Thesaurus, Application Domain, Technology Topic, Popular Technical Reports.
© 2025 PatSnap. All rights reserved.Legal|Privacy policy|Modern Slavery Act Transparency Statement|Sitemap|About US| Contact US: help@patsnap.com