Method for obtaining composite coating by means of laser cladding of extrusion preset powder
A composite coating and pre-powder technology, which is applied in the field of laser cladding to obtain surface composite coating and laser cladding to obtain composite coating, can solve the problems of low coating quality and low powder utilization rate, and achieve simple process , high powder utilization and low cost
- Summary
- Abstract
- Description
- Claims
- Application Information
AI Technical Summary
Problems solved by technology
Method used
Image
Examples
Embodiment 1
[0035] A. Treat the surface of the square base material that needs cladding composite coating: depending on the surface roughness of the base material, perform traditional grinding treatment on it and then clean it with acetone and absolute ethanol to achieve the purpose of degreasing and derusting ;
[0036] B. Powder treatment: put the powder to be clad composed of B and Ti in a vacuum drying oven and dry it at 110°C for 24 hours, and then use polyethylene with a mass percentage concentration of 3% which accounts for 5% of the total mass of the preset layer Alcohol aqueous solution is used as a binder to uniformly mix the powder to be clad into a paste, and use figure 1The extrusion device shown puts the powder to be clad into the extrusion cavity, and pushes the extrusion rod 1a to make the extrusion piston 1b extrude it in the form of a strip (the cross-sectional shape is circular) and preset it on the base material. Surface: Preset one strip on the surface of the substra...
Embodiment 2
[0040] A. Treat the surface of the cylindrical substrate that needs to be clad with a composite coating: depending on the surface roughness of the substrate material, perform special processing and then clean it with acetone and absolute ethanol to achieve the purpose of removing oil and rust ;
[0041] B. Powder treatment: will be made of Al 2 o 3 The cladding powder composed of Ti and Ti was placed in a vacuum drying oven and dried at 100°C for 30 hours, and then the polyvinyl alcohol aqueous solution with a mass percentage concentration of 8% was used as a binder, which accounted for 10% of the total mass of the preset layer. The powder to be clad is evenly mixed and blended into a paste, and used figure 1 The extrusion device shown puts the powder to be clad into the extrusion chamber, and pushes the extrusion rod 1a to make the extrusion piston 1b extrude it in strip form (trapezoidal in cross section) and preset it on the surface of the substrate ; Preset one strip on...
Embodiment 3
[0045] A. Treat the surface of the complex curved cylindrical substrate that needs cladding composite coating: depending on the surface roughness of the substrate material, it is cleaned with acetone and absolute ethanol after special processing to achieve degreasing and rust removal the goal of;
[0046] B. Powder treatment: Put the powder to be clad composed of Ni60 and TiC in a vacuum drying oven and dry it at 120°C for 36 hours, and then use titanium dioxide sol accounting for 2% of the total mass of the preset layer as a binder to melt Cover the powder and mix evenly to form a paste, and use figure 1 The extrusion device shown puts the powder to be clad into the extrusion cavity, and pushes the extrusion rod 1a to make the extrusion piston 1b extrude it in strip form (the cross-sectional shape is rectangular) and preset it on the surface of the substrate ; Preset one strip on the surface of the substrate first, then perform the operations of steps C and D, then preset an...
PUM
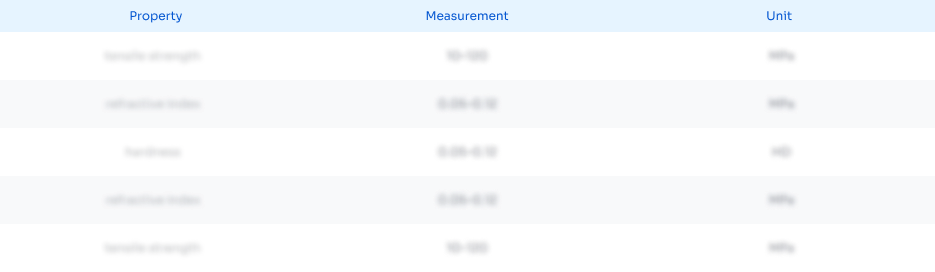
Abstract
Description
Claims
Application Information

- Generate Ideas
- Intellectual Property
- Life Sciences
- Materials
- Tech Scout
- Unparalleled Data Quality
- Higher Quality Content
- 60% Fewer Hallucinations
Browse by: Latest US Patents, China's latest patents, Technical Efficacy Thesaurus, Application Domain, Technology Topic, Popular Technical Reports.
© 2025 PatSnap. All rights reserved.Legal|Privacy policy|Modern Slavery Act Transparency Statement|Sitemap|About US| Contact US: help@patsnap.com