Magnesium alloy with hot cracking resistance and low linear shrinkage
A technology for casting magnesium alloys and linear shrinkage rate, applied in the field of magnesium alloys, can solve the problems affecting the qualification rate of magnesium alloy parts, affecting the application of casting magnesium alloys, limiting the scope of use, etc., and achieves excellent filling ability, liquid volume and solid volume. The effect of small changes and excellent mechanical properties
- Summary
- Abstract
- Description
- Claims
- Application Information
AI Technical Summary
Problems solved by technology
Method used
Examples
Embodiment 1
[0028] The magnesium alloy is prepared according to the steps described in the above process 1, and the casting is cast by a metal mold. The weight percentage composition of the magnesium alloy is Zn 0.2%, Zr 0.0002%, Y 0.0002%, Nb 0.0002%, Al 0.001%, Li 0.0002%, The rest is Mg.
[0029] Castings are heat treated.
[0030] See Table 1 for the properties of the magnesium alloy castings provided in this example.
Embodiment 2
[0032] The magnesium alloy is prepared according to the steps described in the above process 2, and the casting adopts semi-solid casting. The weight percentage composition of the magnesium alloy is Zn 9%, Zr 2%, Sc 16%, Nb 4%, Al 1.49%, Li 9%, and the rest is Mg.
[0033] Castings are heat treated.
[0034] See Table 1 for the properties of the magnesium alloy castings provided in this example.
Embodiment 3
[0036] The magnesium alloy is prepared according to the steps described in the above process 2. The casting adopts high pressure die casting. The weight percentage composition of the magnesium alloy is Zn 0.2%, Zr 0.4%, Sm 0.1%, Nb 0.05%, Al 0.03%, Li 0.01%, and the rest are Mg.
[0037] See Table 1 for the properties of the magnesium alloy castings provided in this example.
PUM
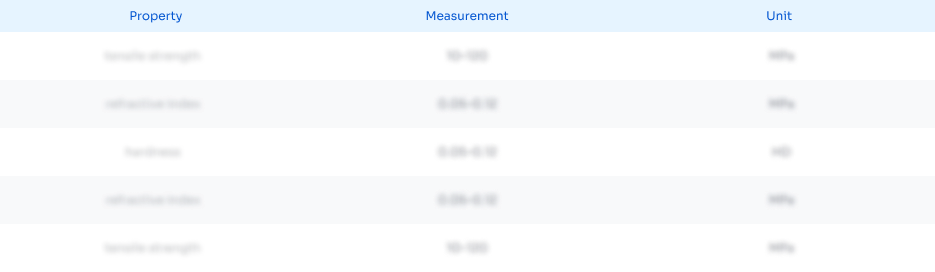
Abstract
Description
Claims
Application Information

- R&D
- Intellectual Property
- Life Sciences
- Materials
- Tech Scout
- Unparalleled Data Quality
- Higher Quality Content
- 60% Fewer Hallucinations
Browse by: Latest US Patents, China's latest patents, Technical Efficacy Thesaurus, Application Domain, Technology Topic, Popular Technical Reports.
© 2025 PatSnap. All rights reserved.Legal|Privacy policy|Modern Slavery Act Transparency Statement|Sitemap|About US| Contact US: help@patsnap.com