Direct graphene film transfer method
A graphene film, a direct technology, applied in the field of nanomaterials, can solve the problems of inconvenient transfer of graphene film, slow pace of practical application of graphene, etc., and achieve the effect of easy industrial application, controllable product size and simple equipment
- Summary
- Abstract
- Description
- Claims
- Application Information
AI Technical Summary
Problems solved by technology
Method used
Image
Examples
Embodiment 1
[0021] Example 1: The graphene film on the copper foil is transferred to a circular hole carrier screen.
[0022] Such as figure 1 As shown in the flow chart, firstly, a graphene film is grown on a 25-micron thick copper foil using a CVD device; then an oxygen plasma cleaner is used to clean the graphene on one side of the copper foil. The cleaning voltage is 650V and the cleaning time is 3 minutes. , To obtain a combination of a single-layer graphene film and a copper foil; then flatly affix the circular hole carrier net on the single-layer graphene film, and add 5 mL isopropanol to the edge of the carrier net to make the carrier net and the graphene film fully contact , The aperture of the carrier net is 1 micron; then the combination of the round hole carrier net, graphene film and copper foil is immersed in a ferric chloride aqueous solution with a molar mass of 0.5 mol / L, and the copper foil is completely corroded after 40 minutes; The combination of the round hole carrier n...
Embodiment 2
[0023] Example 2: Transfer the graphene film on the copper foil to the elliptical carrier net.
[0024] The specific steps are similar to those in Example 1, but the transfer carrier is an elliptical carrier net, and the scanned image is as Figure 5 As shown, the size of the complete graphene film reaches about 100 microns.
Embodiment 3
[0025] Example 3: Transfer the graphene film on the copper foil to the silica substrate.
[0026] The specific steps are similar to Example 1, but the transfer carrier is a silica substrate. In step 4, the silica substrate needs to be suspended and fixed so that the combination of the silica substrate, graphene film and copper foil is tightly attached to the surface of the etching solution .
PUM
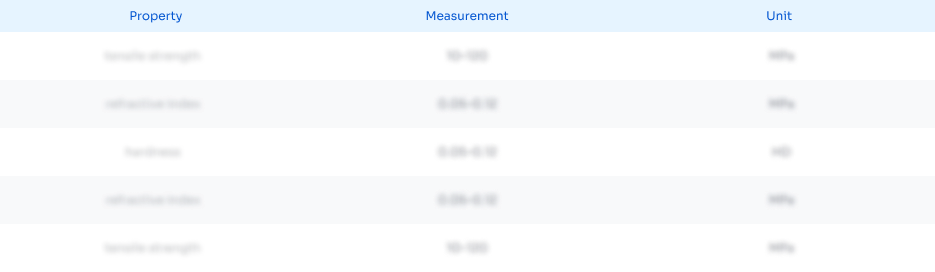
Abstract
Description
Claims
Application Information

- R&D Engineer
- R&D Manager
- IP Professional
- Industry Leading Data Capabilities
- Powerful AI technology
- Patent DNA Extraction
Browse by: Latest US Patents, China's latest patents, Technical Efficacy Thesaurus, Application Domain, Technology Topic, Popular Technical Reports.
© 2024 PatSnap. All rights reserved.Legal|Privacy policy|Modern Slavery Act Transparency Statement|Sitemap|About US| Contact US: help@patsnap.com