Flux production process for submerged arc welding
A production process, submerged arc welding technology, applied in the direction of welding medium, manufacturing tools, welding equipment, etc., can solve the problems of reducing production efficiency, increasing flux costs, prone to porosity, etc., to improve production efficiency and product performance, reduce raw materials Cost, the effect of avoiding the oxidation of iron powder
- Summary
- Abstract
- Description
- Claims
- Application Information
AI Technical Summary
Problems solved by technology
Method used
Image
Examples
Embodiment 1
[0018] Flux production process for submerged arc welding, including the following steps:
[0019] ①. Ingredients: equipped with flux raw materials, the parts by weight of various components in the flux raw materials are: CaF 2 : 5, MgO: 30, Al 2 o 3 : 12, SiO 2 : 10, CaO: 8, MnO: 5, and impurities, adding iron powder that is 25 parts by weight in the raw materials provided;
[0020] ② Stirring: Prepare the raw materials into powder, after re-pounding, put them into the mixer for dry mixing, after mixing evenly, add the binder and put them into the wet mixer for wet mixing;
[0021] ③, granulation, drying, screening: Put the evenly stirred raw materials into the granulator for granulation, then dry the granulation and screen out the particles within the standard particle size range;
[0022] ④. Sintering: Send the particles into the sintering furnace, and sinter for 40 minutes at a temperature of 350 ° C. During sintering, argon gas with a flow rate of 0.5 liters / min is int...
Embodiment 2
[0026] Flux production process for submerged arc welding, including the following steps:
[0027] ①. Ingredients: equipped with flux raw materials, the parts by weight of various components in the flux raw materials are: CaF 2 : 7, MgO: 25, Al 2 o 3 : 9, SiO 2 : 13, CaO: 12, MnO: 8, and impurities, adding iron powder that is 32 parts by weight in the raw materials provided;
[0028] ② Stirring: Prepare the raw materials into powder, after re-pounding, put them into the mixer for dry mixing, after mixing evenly, add the binder and put them into the wet mixer for wet mixing;
[0029] ③, granulation, drying, screening: Put the evenly stirred raw materials into the granulator for granulation, then dry the granulation and screen out the particles within the standard particle size range;
[0030] ④. Sintering: Send the particles into the sintering furnace, and sinter for 30 minutes at a temperature of 550°C. During sintering, argon gas with a flow rate of 0.1 liter / min is introd...
Embodiment 3
[0034] Flux production process for submerged arc welding, including the following steps:
[0035] ①. Ingredients: equipped with flux raw materials, the parts by weight of various components in the flux raw materials are: CaF 2 : 10, MgO: 20, Al 2 o 3 : 6, SiO 2 : 16, CaO: 17, MnO: 5, and impurities, adding iron powder that is 40 parts by weight in the raw materials provided;
[0036] ② Stirring: Prepare the raw materials into powder, after re-pounding, put them into the mixer for dry mixing, after mixing evenly, add the binder and put them into the wet mixer for wet mixing;
[0037] ③, granulation, drying, screening: Put the evenly stirred raw materials into the granulator for granulation, then dry the granulation and screen out the particles within the standard particle size range;
[0038] ④. Sintering: Send the particles into the sintering furnace, and sinter for 36 minutes at a temperature of 450 ° C. During sintering, argon gas with a flow rate of 1 liter / min is intro...
PUM
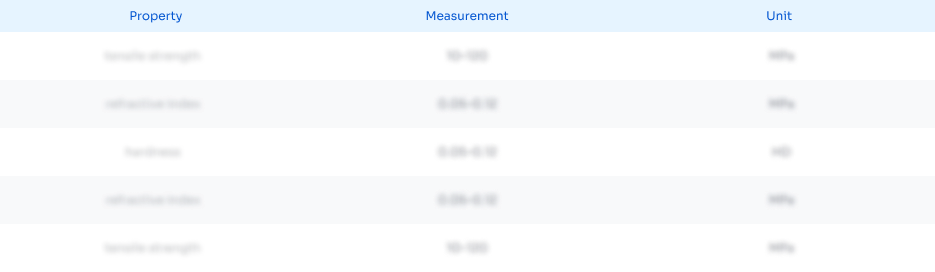
Abstract
Description
Claims
Application Information

- R&D
- Intellectual Property
- Life Sciences
- Materials
- Tech Scout
- Unparalleled Data Quality
- Higher Quality Content
- 60% Fewer Hallucinations
Browse by: Latest US Patents, China's latest patents, Technical Efficacy Thesaurus, Application Domain, Technology Topic, Popular Technical Reports.
© 2025 PatSnap. All rights reserved.Legal|Privacy policy|Modern Slavery Act Transparency Statement|Sitemap|About US| Contact US: help@patsnap.com