Polyethylene heat shrinkable film gravure printing process
A gravure printing process and heat shrinkable film technology, applied in gravure rotary printing presses, printing, printing presses, etc., can solve the problems of large printing loss, low qualified rate of finished products, difficult to increase the output of finished products, etc., and can improve the environmental temperature. Effect
- Summary
- Abstract
- Description
- Claims
- Application Information
AI Technical Summary
Problems solved by technology
Method used
Image
Examples
Embodiment Construction
[0032] The present invention will be described in further detail below in conjunction with the accompanying drawings and specific embodiments, and the implementation scope of the present invention is not limited thereto.
[0033] Such as figure 1 As shown, a kind of polyethylene heat-shrinkable film gravure printing process described in this embodiment comprises the following steps:
[0034] (1) Unwinding of polyethylene heat shrinkable film;
[0035] (2), unwinding traction;
[0036] (3) Inking the ink transfer roller;
[0037] (4), scraping ink with scraper;
[0038] (5), gravure printing;
[0039] (6), ink drying;
[0040] (7), printed matter cooling;
[0041] (8), multi-color group overprinting, including repeating steps (3), (4), (5), (6) and (7) several times in sequence;
[0042] (9), winding traction;
[0043] (10), winding;
[0044] (11) Quality inspection;
[0045] (12), subsection;
[0046] (13), sealing and cutting;
[0047] (14) Finished product packag...
PUM
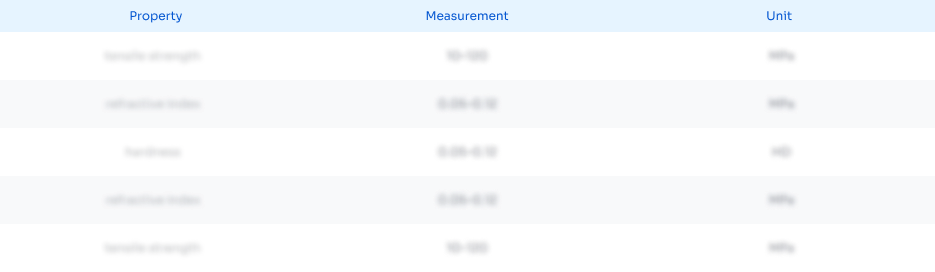
Abstract
Description
Claims
Application Information

- Generate Ideas
- Intellectual Property
- Life Sciences
- Materials
- Tech Scout
- Unparalleled Data Quality
- Higher Quality Content
- 60% Fewer Hallucinations
Browse by: Latest US Patents, China's latest patents, Technical Efficacy Thesaurus, Application Domain, Technology Topic, Popular Technical Reports.
© 2025 PatSnap. All rights reserved.Legal|Privacy policy|Modern Slavery Act Transparency Statement|Sitemap|About US| Contact US: help@patsnap.com