High-efficiency low-cost purification process of flue gas
A purification process and flue gas technology, used in chemical instruments and methods, dispersed particle separation, separation methods, etc., can solve problems such as unsatisfactory treatment efficiency, unintegrated treatment processes, and difficult removal of toxic organics, and achieves easy treatment and Effects of detoxification, reduction of processing load and equipment size, and processing cost savings
- Summary
- Abstract
- Description
- Claims
- Application Information
AI Technical Summary
Problems solved by technology
Method used
Image
Examples
Embodiment 1
[0039] Now we are dealing with the flue gas of a company’s self-provided power plant. In terms of volume fraction, it contains CO 2 11.2%, O 2 8.49%, N 2 54%, H 2 O is 24%, SO 2 1509 mg / m 3 , NOx is 1212mg / m 3 , and the rest are other trace pollutants and soot. The flue gas flow rate is 1124980 m 3 / h, the flue gas temperature is 220°C. Using the above process, the flue gas enters the waste heat exchanger E0 through the pipeline 1, so that the temperature of the flue gas is reduced from 220°C to 115°C, and hot water is produced at the same time, and 350t / h liquid water with a temperature of 88°C can be obtained. Hot water storage tank for hot water users. Subsequently, the flue gas enters the lower part of the comprehensive washing tower T1 from the upper part of the waste heat exchanger E0 through the pipeline 2, and contacts with the first circulating liquid, the second circulating liquid and the third circulating liquid which flow countercurrently in stages, and sim...
Embodiment 2
[0046] Now we are dealing with the flue gas of domestic waste incineration with a processing capacity of 360t / d in a company. In terms of volume fraction, it contains CO 2 12.4%, O 2 7.63%, N 2 56.2%, H 2 O is 20.8%, SOx is 1434 mg / m 3 , NOx is 1056mg / m 3 , and the rest are other trace pollutants and soot. Flue gas flow rate is 45080 m 3 / h, the flue gas temperature is 120°C (has been cooled). Using the above process method, the flue gas enters the waste heat exchanger E0 through the pipeline 1, so that the temperature of the flue gas is reduced from 120°C to 85°C, and hot water is produced at the same time, and 8t / h liquid water with a temperature of 64°C can be obtained. Hot water storage tank for hot water users. Subsequently, the flue gas enters the lower part of the comprehensive scrubber T1 from the upper part of the waste heat exchanger E0 through the pipeline 2, and contacts with the first circulating liquid, the second circulating liquid and the third circulati...
Embodiment 3
[0053] Now we are dealing with the flue gas of domestic waste incineration with a processing capacity of 360t / d in a company. In terms of volume fraction, it contains CO 2 12.4%, O 2 7.63%, N 2 56.2%, H 2 O is 20.8%, SOx is 1434 mg / m 3 , NOx is 1056mg / m 3 , and the rest are other trace pollutants and soot. Flue gas flow rate is 45080 m 3 / h, the flue gas temperature is 120°C (has been cooled). Using the above process method, the flue gas enters the waste heat exchanger E0 through the pipeline 1, so that the temperature of the flue gas is reduced from 120°C to 85°C, and hot water is produced at the same time, and 8t / h liquid water with a temperature of 64°C can be obtained. Hot water storage tank for hot water users. Subsequently, the flue gas enters the lower part of the comprehensive scrubber T1 from the upper part of the waste heat exchanger E0 through the pipeline 2, and contacts with the first circulating liquid, the second circulating liquid and the third circulati...
PUM
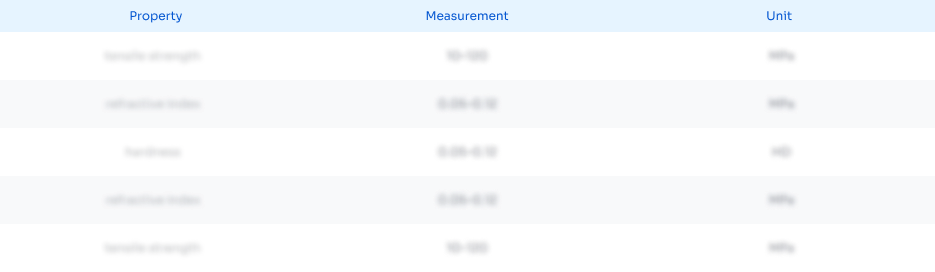
Abstract
Description
Claims
Application Information

- R&D
- Intellectual Property
- Life Sciences
- Materials
- Tech Scout
- Unparalleled Data Quality
- Higher Quality Content
- 60% Fewer Hallucinations
Browse by: Latest US Patents, China's latest patents, Technical Efficacy Thesaurus, Application Domain, Technology Topic, Popular Technical Reports.
© 2025 PatSnap. All rights reserved.Legal|Privacy policy|Modern Slavery Act Transparency Statement|Sitemap|About US| Contact US: help@patsnap.com