Method for preparing micro/nano porous ceramic fibers by low-temperature electrostatic spinning
An electrospinning and nanoporous technology, applied in the field of material preparation, can solve the problems of small specific surface area of micro- and nanoporous ceramic fibers, and achieve the effect of high specific surface area and broad application prospects
- Summary
- Abstract
- Description
- Claims
- Application Information
AI Technical Summary
Problems solved by technology
Method used
Image
Examples
Embodiment 1
[0041] First, 3.5g of polystyrene was dissolved in 90g of camphene, then 6.5g of butyl phthalate was added, and the spinning solution was obtained after stirring and aging; the spinning solution was poured into a syringe, and the ambient temperature of low-temperature electrospinning was 0°C. The relative partial pressure of the camphene vapor is 90%, the voltage in the spinning process is 40kV, the collection distance is 30cm, and the spinning solution propulsion speed is 2.5ml / h, and the composite fiber is spun out, and the composite fiber is made of butyl phthalate, polyester It is composed of styrene and camphene crystals; then dried in an environment of 660Pa to obtain composite porous fibers, which are composed of butyl phthalate and polystyrene; the composite porous fibers are sintered at 1200°C to obtain micro and nano TiO 2 Porous fibers.
Embodiment 2
[0043]First, dissolve 19.5g of polyvinyl alcohol in 70g of deionized water, then add 10.5g of zinc nitrate, stir and age to obtain a spinning solution; pour the spinning solution into a syringe, and the temperature of the low-temperature electrospinning environment is -20°C. The relative partial pressure of the steam is 40%, the voltage during the spinning process is 23kV, the collection distance is 10cm, the spinning solution propulsion speed is 0.5ml / h, and the composite fiber is obtained by spinning. The composite fiber is composed of zinc nitrate, polyvinyl alcohol and ice crystals. Composition; then drying in an environment of 50Pa to obtain a composite porous fiber, the composite porous fiber is composed of zinc nitrate and polyvinyl alcohol; the composite porous fiber is sintered at 1200 ° C to obtain micro-nano ZnO porous fiber.
Embodiment 3
[0045] First, dissolve 20g of polyvinylpyrrolidone in 60g of tert-butanol, then add 20g of tetraethyl orthosilicate, stir and age to obtain a spinning solution; pour the spinning solution into a syringe, and the ambient temperature of low-temperature electrospinning is -40°C , the relative partial pressure of tert-butanol vapor is 50%, the voltage during the spinning process is 10kV, the collection distance is 15cm, the spinning solution propulsion speed is 1ml / h, and the composite fiber is obtained by spinning. ester, polyvinylpyrrolidone and tert-butanol crystals; then dry in an environment of 120Pa to obtain a composite porous fiber, which is composed of tetraethyl orthosilicate and polyvinylpyrrolidone; the composite porous fiber is sintered at 800 ° C , to obtain micro- and nano-SiO 2 Porous fibers.
PUM
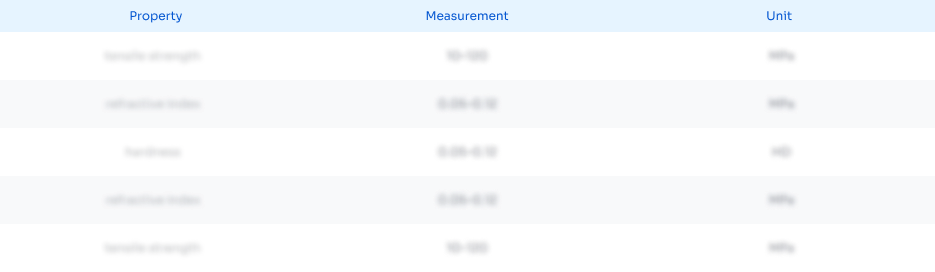
Abstract
Description
Claims
Application Information

- R&D
- Intellectual Property
- Life Sciences
- Materials
- Tech Scout
- Unparalleled Data Quality
- Higher Quality Content
- 60% Fewer Hallucinations
Browse by: Latest US Patents, China's latest patents, Technical Efficacy Thesaurus, Application Domain, Technology Topic, Popular Technical Reports.
© 2025 PatSnap. All rights reserved.Legal|Privacy policy|Modern Slavery Act Transparency Statement|Sitemap|About US| Contact US: help@patsnap.com