Tunnel kiln
A technology of tunnel kiln and gas channel, which is applied in the field of tunnel kiln, can solve the problems of increasing time-consuming temperature rise in sintering section, long time-consuming temperature rising in sintering section, limited drying heating capacity, etc., and achieve the effect of high temperature, short sintering time-consuming, and convenient complete combustion
- Summary
- Abstract
- Description
- Claims
- Application Information
AI Technical Summary
Problems solved by technology
Method used
Image
Examples
Embodiment Construction
[0019] This embodiment is a straight tunnel kiln, the inner wall of the tunnel is laid with refractory insulation materials, and the bottom has guide rails for refractory brick transport vehicles, including kiln head door 1, front hanging door opening 3, hot gas valve 4, middle hanging door opening 5, heating Air pipe tee 6, hot gas flow meter 7, rear hanging door hole 8, gas flow meter 10, hot gas channel 11, hot gas blower 12, suction port 13, kiln tail door 14, rear hanging door 16, combustion chamber 17, flue gas nozzle 18. Flue gas passage 19, flue gas meter 21, middle hanging door 22, heat recovery section 23, front hanging door 24, waste heat valve 26, waste heat gas passage 27 and monitor 29, of which:
[0020] Along the depth direction of tunnel kiln 2, there are kiln head door 1, kiln entry section 28, preheating section 25, reheating section 23, sintering section 20, cooling section 15 and kiln tail door 14, in which the tunnel kiln preheating The section is divided...
PUM
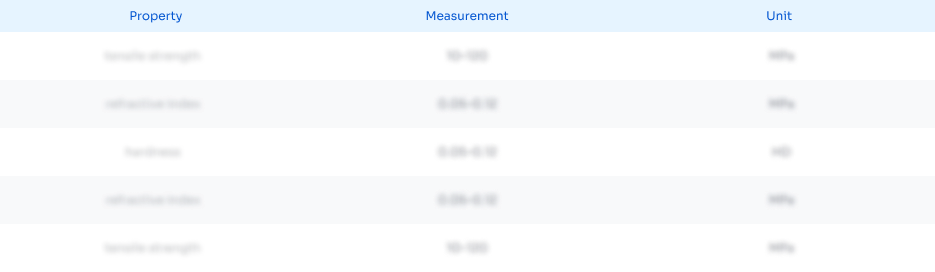
Abstract
Description
Claims
Application Information

- R&D
- Intellectual Property
- Life Sciences
- Materials
- Tech Scout
- Unparalleled Data Quality
- Higher Quality Content
- 60% Fewer Hallucinations
Browse by: Latest US Patents, China's latest patents, Technical Efficacy Thesaurus, Application Domain, Technology Topic, Popular Technical Reports.
© 2025 PatSnap. All rights reserved.Legal|Privacy policy|Modern Slavery Act Transparency Statement|Sitemap|About US| Contact US: help@patsnap.com