Compression bar type passive low-frequency three-dimensional vibration isolator
A compression rod type and vibration isolator technology, which is applied in the direction of shock absorbers, shock absorber-spring combinations, shock absorbers, etc., can solve problems such as vibration isolation, and achieve high stability
- Summary
- Abstract
- Description
- Claims
- Application Information
AI Technical Summary
Problems solved by technology
Method used
Image
Examples
Embodiment 1
[0027] see figure 1 , the bar-type passive low-frequency three-way vibration isolator includes a barrel-shaped base 7, and more than three lower elastic elements 6 are evenly installed in the base 7 through splints 13, and the lower elastic elements 6 are wire rope springs. The diameter, number of strands, length, number of turns, winding method and degree of tightness are used to design the required bearing capacity, stiffness and damping in the vertical direction. An annular step is provided on the side wall of the opening end of the upper part of the base 7, and four guide grooves 11 along the axial direction are evenly distributed on the inner wall of the base 7 at the lower part of the annular step, see Figure 4 ; The top of the lower elastic element 6 is provided with a circular support platform 5, and four guide blocks 12 are evenly distributed on the circumference of the support platform 5, see Figure 5 , the four guide blocks 12 and the four guide grooves 11 are co...
Embodiment 2
[0031] see figure 2 , and the main difference of embodiment 1 is that: support platform 5 middle part is provided with through hole, and center guide rod 14 passes through the through hole of support platform 5 and is connected with upper baffle plate 4 at the upper end, and the lower end is connected with base 7; support platform 5 and upper The upper elastic element 17 is set on the center guide rod 14 between the baffle plates 4, and the lower elastic element 6 is set on the center guide rod 14 between the support table 5 and the base 7, and the upper elastic element 17 and the lower elastic element 6 are both coil spring. Limiting ring 16 is respectively installed on the top surface of the support table 5 corresponding to the upper end and the lower end of the upper elastic element 17 and the bottom surface of the upper baffle plate 4; Limiting rings 16 are respectively installed on the bottom surface of the base 7 . The annular elastic element 8 is made of rubber. Oth...
Embodiment 3
[0033] see image 3, and the main difference of embodiment 3 is: the material of the lower elastic element 6 and the upper elastic element 17 are both rubber-metal composite springs; the material of the annular elastic element 8 is rubber-steel rope composite spring. Others are with embodiment 2. Mainly on the basis of embodiment 2, the damping and bearing capacity of the vibration isolator are increased, and it is mainly used in a vibration isolation system where low-frequency vibration isolation requirements are not too strict.
PUM
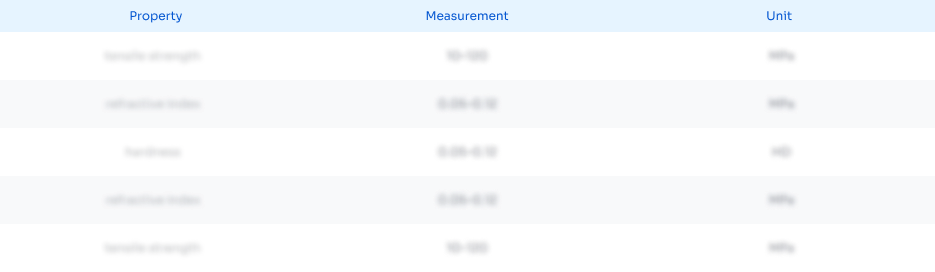
Abstract
Description
Claims
Application Information

- Generate Ideas
- Intellectual Property
- Life Sciences
- Materials
- Tech Scout
- Unparalleled Data Quality
- Higher Quality Content
- 60% Fewer Hallucinations
Browse by: Latest US Patents, China's latest patents, Technical Efficacy Thesaurus, Application Domain, Technology Topic, Popular Technical Reports.
© 2025 PatSnap. All rights reserved.Legal|Privacy policy|Modern Slavery Act Transparency Statement|Sitemap|About US| Contact US: help@patsnap.com