Continuous preparation method of silicon boron nitrogen-based ceramic fiber
A ceramic fiber, nitrogen-based technology is applied in the field of preparation of continuous silicon-boron-nitrogen-based ceramic fibers, which can solve the problem of not showing real objects, and achieve the effects of improving anti-oxidation performance, inhibiting the introduction of oxygen elements, and low cost of raw materials
- Summary
- Abstract
- Description
- Claims
- Application Information
AI Technical Summary
Problems solved by technology
Method used
Image
Examples
Embodiment 1
[0019] The precursor polymer polysilazaborane (PBSZ) is isolated from air and moisture for melt spinning, the spinning temperature is 130°C, and the winding speed is 200m / min; the precursor polymer fiber is placed in a continuous cracking furnace, Introduce a mixed gas with a volume ratio of ammonia and nitrogen of 70:30, raise the temperature to 280°C at a rate of 0.5°C / min, keep it warm for 2 hours, and perform non-melting treatment at a speed of 0.6mm / min; The fibers were further placed in a continuous high-temperature furnace, and a mixed gas with a volume ratio of ammonia and nitrogen of 70:30 was introduced, and the temperature was raised to 600°C at a rate of 0.5°C / min. The heating rate of ℃ / min was raised to 1000 ℃, kept for 4 hours, then raised to 1600 ℃ at a rate of 1 ℃ / min, kept for 2 hours, and then lowered to room temperature to obtain continuous SiNB ceramic fibers. The C% in the ceramic fiber is 0.1% (see Table 1), which can withstand a temperature of 1500°C in ...
Embodiment 2
[0023] The precursor polymer polysilazaborane (PBSZ) is isolated from air and moisture for melt spinning, the spinning temperature is 150°C, and the winding speed is 200m / min; the precursor polymer fiber is placed in a continuous cracking furnace, Introduce a mixed gas with a volume ratio of ammonia and nitrogen of 90:10, raise the temperature to 280°C at a rate of 1°C / min, keep it warm for 2 hours, and perform non-melting treatment at a speed of 0.6mm / min; The fibers were further placed in a continuous high-temperature furnace, and a mixed gas with a volume ratio of ammonia and nitrogen of 80:20 was introduced, and the temperature was raised to 600°C at a rate of 2°C / min. The heating rate of ℃ / min was raised to 1000 ℃, kept for 5 hours, then raised to 1600 ℃ at a rate of 3 ℃ / min, kept for 6 hours, and then lowered to room temperature to obtain continuous SiNB ceramic fibers. The C% in the ceramic fiber is 0.05%, and it can withstand the temperature of 1500°C in air and 1700°C...
Embodiment 3
[0025] The precursor polymer polysilazaborane (PBSZ) is isolated from air and moisture for melt spinning, the spinning temperature is 250°C, and the winding speed is 800m / min; the precursor polymer fiber is placed in a continuous cracking furnace, Introduce a mixed gas with a volume ratio of ammonia and nitrogen of 50:50, raise the temperature to 280°C at a rate of 0.5°C / min, keep it warm for 3 hours, and perform non-melting treatment at a speed of 0.6mm / min; The fibers were further placed in a continuous high-temperature furnace, and a mixed gas with a volume ratio of ammonia and nitrogen of 50:50 was introduced, and the temperature was raised to 600°C at a rate of 1°C / min. Raise the temperature up to 1000°C at a rate of ~5°C / min, hold for 2 hours, then raise the temperature to 1600°C at a rate of 5°C / min, hold for 8 hours, and cool down to room temperature to obtain continuous SiNB ceramic fibers. The C% in the ceramic fiber is 1.0%, and it can withstand the temperature of 1...
PUM
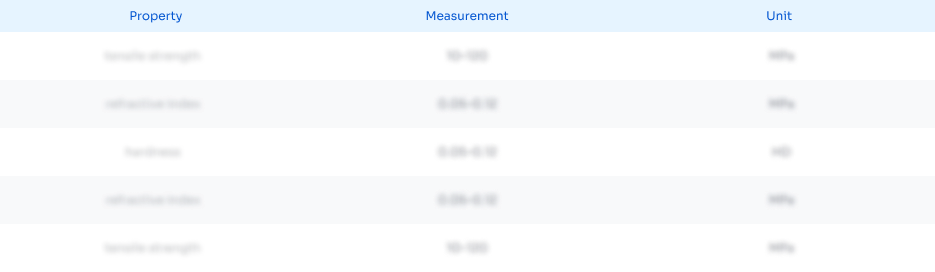
Abstract
Description
Claims
Application Information

- Generate Ideas
- Intellectual Property
- Life Sciences
- Materials
- Tech Scout
- Unparalleled Data Quality
- Higher Quality Content
- 60% Fewer Hallucinations
Browse by: Latest US Patents, China's latest patents, Technical Efficacy Thesaurus, Application Domain, Technology Topic, Popular Technical Reports.
© 2025 PatSnap. All rights reserved.Legal|Privacy policy|Modern Slavery Act Transparency Statement|Sitemap|About US| Contact US: help@patsnap.com