Aircraft wing box using grid structure and design method
A grid structure, wing box technology, applied in the direction of wings, aircraft parts, instruments, etc., can solve the problem of unable to achieve efficient combination of weight reduction and load
- Summary
- Abstract
- Description
- Claims
- Application Information
AI Technical Summary
Problems solved by technology
Method used
Image
Examples
Embodiment Construction
[0025] The present invention is described in further detail below collection accompanying drawing:
[0026] Such as figure 1 , figure 2 shown
[0027] Part of the box section of the composite grid structure has a first-order natural frequency of 187.8Hz under the four-sided fixed-support boundary condition. The ply angle is optimized. Taking the first-order natural frequency of part of the box section as the objective function, and taking the ply angles of the 16 single layers of the grid structure skin and the 8 single layers of the grid part as the design variables, the optimal design is carried out.
[0028] optimization process.
[0029] Before the optimization analysis, the type of analysis condition should be filled in the bdf file. For modal optimization, the SOL 103 solver should be used for analysis in the bdf statement, and the bdf segment is ANALYSIS=MODES.
[0030] 1. Associated Design Variables
[0031] Nastran cards are statements written in the bdf file i...
PUM
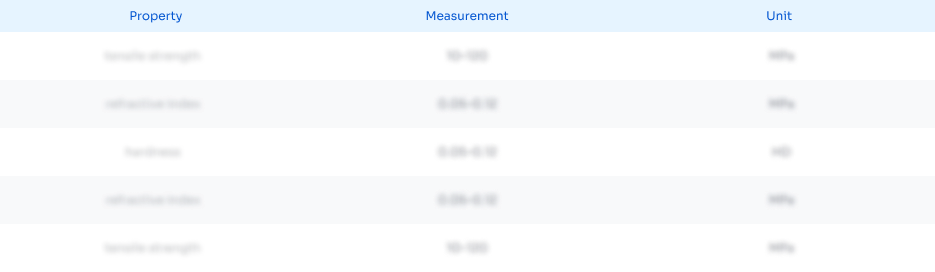
Abstract
Description
Claims
Application Information

- Generate Ideas
- Intellectual Property
- Life Sciences
- Materials
- Tech Scout
- Unparalleled Data Quality
- Higher Quality Content
- 60% Fewer Hallucinations
Browse by: Latest US Patents, China's latest patents, Technical Efficacy Thesaurus, Application Domain, Technology Topic, Popular Technical Reports.
© 2025 PatSnap. All rights reserved.Legal|Privacy policy|Modern Slavery Act Transparency Statement|Sitemap|About US| Contact US: help@patsnap.com