Method for manufacturing shape memory polymer core mold by winding composite material component
A composite material component and memory polymer technology, which is applied in the field of manufacturing a shape memory polymer core mold for composite material component winding molding, can solve the problem that the core mold assembly, dismantling and deformation cannot meet the composite material winding technology, and the application range is limited. Limitation, brittle gypsum layer, etc., to avoid manual assembly and disassembly procedures, obvious economic benefits, and short production cycle.
- Summary
- Abstract
- Description
- Claims
- Application Information
AI Technical Summary
Problems solved by technology
Method used
Image
Examples
Embodiment 1
[0029] Preparation of shape memory polymer mandrel for composite pressure vessel winding molding:
[0030] Step 1, prepare the hydrogenated epoxy resin system: put the hydrogenated epoxy resin, hexanediol diglycidyl ether and maleic anhydride into a vacuum drying oven after mixing uniformly in a molar ratio of 0.9:0.1:2.0, and put them in a vacuum oven at a temperature of Remove bubbles at 55°C for 10 minutes to obtain a hydrogenated epoxy resin system;
[0031] Step 2. Making hydrogenated epoxy resin blanks: pour the hydrogenated epoxy resin system described in step 1 into a cylindrical mold, then place the poured mold in an oven to solidify, and demould after cooling to room temperature to obtain a hydrogenated ring Oxygen resin blank; the curing system is: curing at a temperature of 80°C for 3 hours, then at a temperature of 120°C for 3 hours, and finally at a temperature of 180°C for 1 hour; figure 1 As shown, the cylindrical mold is formed by connecting a cylindrical mal...
Embodiment 2
[0036] Preparation of shape memory polymer mandrel for composite pipe winding molding:
[0037] Step 1, prepare the hydrogenated epoxy resin system: put the hydrogenated epoxy resin, hexanediol diglycidyl ether and maleic anhydride into a vacuum drying oven after mixing uniformly in a molar ratio of 0.6:0.3:2.0, and put them in a vacuum oven at a temperature of Remove bubbles at 50°C for 5 minutes to obtain a hydrogenated epoxy resin system;
[0038] Step 2. Making hydrogenated epoxy resin blanks: pour the hydrogenated epoxy resin system described in step 1 into a cylindrical mold, then place the poured mold in an oven to solidify, and demould after cooling to room temperature to obtain a hydrogenated ring Oxygen resin blank; the curing system is: curing at a temperature of 65°C for 3 hours, then at a temperature of 120°C for 3 hours, and finally at a temperature of 150°C for 1 hour; figure 1 As shown, the cylindrical mold is formed by connecting a cylindrical male mold 1 and...
Embodiment 3
[0043] Preparation of shape memory polymer mandrel for composite pressure vessel winding molding:
[0044] Step 1. Preparation of hydrogenated epoxy resin system: mix hydrogenated epoxy resin and maleic anhydride in a molar ratio of 1.0:2.0, put them in a vacuum drying oven, and remove air bubbles for 15 minutes at a temperature of 60°C. Obtain hydrogenated epoxy resin system;
[0045] Step 2. Making hydrogenated epoxy resin blanks: pour the hydrogenated epoxy resin system described in step 1 into a cylindrical mold, then place the poured mold in an oven to solidify, and demould after cooling to room temperature to obtain a hydrogenated ring Oxygen resin blank; the curing system is: curing at a temperature of 60°C for 4 hours, then at a temperature of 110°C for 4 hours, and finally at a temperature of 160°C for 1.5 hours; figure 1 As shown, the cylindrical mold is formed by connecting a cylindrical male mold 1 and a cylindrical female mold 2 by bolts;
[0046] Step 3, making...
PUM
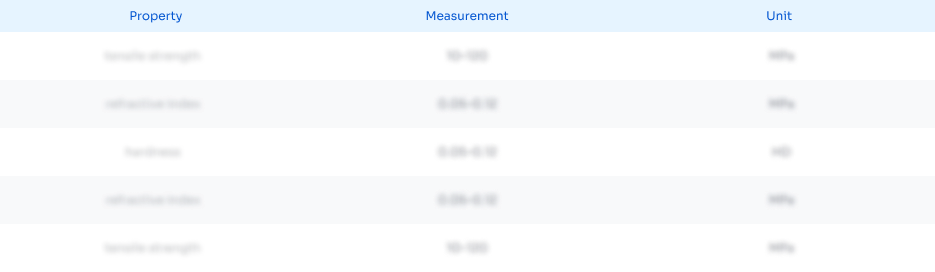
Abstract
Description
Claims
Application Information

- Generate Ideas
- Intellectual Property
- Life Sciences
- Materials
- Tech Scout
- Unparalleled Data Quality
- Higher Quality Content
- 60% Fewer Hallucinations
Browse by: Latest US Patents, China's latest patents, Technical Efficacy Thesaurus, Application Domain, Technology Topic, Popular Technical Reports.
© 2025 PatSnap. All rights reserved.Legal|Privacy policy|Modern Slavery Act Transparency Statement|Sitemap|About US| Contact US: help@patsnap.com