Motor stator punching sheet laminating technology
A motor stator and punching technology, which is applied in the field of punching and stacking technology of motor stators, can solve problems such as the stator axis line is not straight, and achieve the effects of improving motor efficiency, strengthening management, and significant economic benefits
- Summary
- Abstract
- Description
- Claims
- Application Information
AI Technical Summary
Problems solved by technology
Method used
Image
Examples
Embodiment 1
[0020] Follow the steps below:
[0021] 1. During the punching process of the silicon steel strip, under the control of the punching setting screen, place multiple punches of the same column made of the same silicon steel strip, and automatically mark on the punching sheet;
[0022] 2. According to the total height of the stator, the stator punching is divided into even parts; the less the number of pieces in each part, the straighter the axis line of the stator after completion.
[0023] 3. When stacking, the stamping surface is always upward, and according to the pre-programmed mark orientation, each part of this embodiment is stacked after being rotated 180 degrees with the next next part, so that it is stacked in sequence to a specified height.
PUM
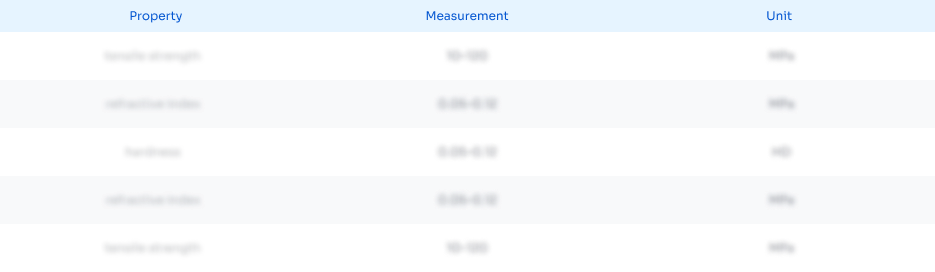
Abstract
Description
Claims
Application Information

- R&D
- Intellectual Property
- Life Sciences
- Materials
- Tech Scout
- Unparalleled Data Quality
- Higher Quality Content
- 60% Fewer Hallucinations
Browse by: Latest US Patents, China's latest patents, Technical Efficacy Thesaurus, Application Domain, Technology Topic, Popular Technical Reports.
© 2025 PatSnap. All rights reserved.Legal|Privacy policy|Modern Slavery Act Transparency Statement|Sitemap|About US| Contact US: help@patsnap.com