Method for curing ceramic slurry by controlling sustained release of high-valence counter ions through temperature
A technology of ceramic slurry and temperature control, which is applied in the field of solidification of inorganic non-metallic ceramics, can solve the problems of long curing time and easy cracks, and achieve the effects of simple operation, avoiding cracking and facilitating industrial production
- Summary
- Abstract
- Description
- Claims
- Application Information
AI Technical Summary
Problems solved by technology
Method used
Image
Examples
Embodiment 1
[0025] 5g / L calcium iodate solidifies 50vol% Al dispersed in 0.2wt% ammonium citrate 2 o 3 slurry.
[0026] 50vol% Al dispersed in 0.2wt% ammonium citrate and fully ball milled at 10°C 2 o 3 Add 0.5g of calcium iodate to 100ml of slurry, mix ball mill for 20min, exhaust and inject mold, treat in water bath at 65-70℃ for 1h-2h, demould, dry at 80℃ for 24h, then heat up at 5℃ / min to 1500-1550℃ for 2h Sintering to obtain a ceramic sintered body.
Embodiment 2
[0028] 6.25g / L calcium iodate solidifies 50vol% Al dispersed in 0.3wt% ammonium citrate 2 o 3 slurry.
[0029] 50vol% Al dispersed in 0.3wt% ammonium citrate and fully ball milled at 10°C 2 o 3 Add 0.625g of calcium iodate to 100ml of slurry, mix ball mill for 20min, exhaust and inject mold, treat in water bath at 60~70℃ for 1h~2h, demould, dry at 80℃ for 24h, then raise temperature at 5℃ / min to 1500~1550℃ for 2h Sintering to obtain a ceramic sintered body.
Embodiment 3
[0031] 7.5g / L calcium iodate solidifies 50vol% Al dispersed in 0.4wt% ammonium citrate 2 o 3 slurry.
[0032] 50vol% Al dispersed in 0.4wt% ammonium citrate and fully ball milled at 10°C 2 o 3 Add 0.75g of calcium iodate to 100ml of slurry, mix ball mill for 20min, exhaust and inject mold, treat in water bath at 60~70℃ for 1h~2h, demould, dry at 80℃ for 24h, then heat up at 5℃ / min to 1500~1550℃ for 2h Sintering to obtain a ceramic sintered body.
PUM
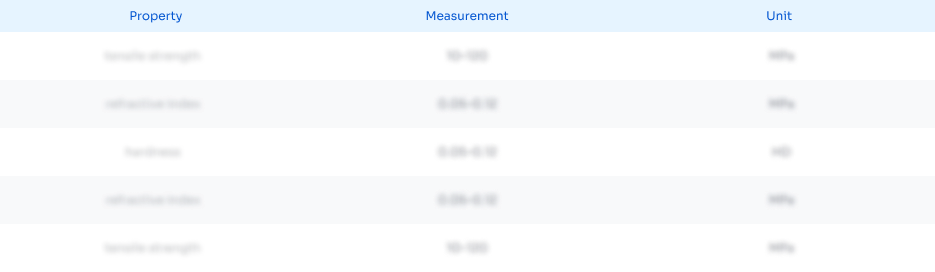
Abstract
Description
Claims
Application Information

- R&D
- Intellectual Property
- Life Sciences
- Materials
- Tech Scout
- Unparalleled Data Quality
- Higher Quality Content
- 60% Fewer Hallucinations
Browse by: Latest US Patents, China's latest patents, Technical Efficacy Thesaurus, Application Domain, Technology Topic, Popular Technical Reports.
© 2025 PatSnap. All rights reserved.Legal|Privacy policy|Modern Slavery Act Transparency Statement|Sitemap|About US| Contact US: help@patsnap.com