Process for producing barium sulfate byproduct in process of removing barium from yellow water
A production process, barium sulfate technology, applied in the direction of calcium/strontium/barium sulfate, calcium carbonate/strontium/barium, etc., can solve the problems of slow natural sedimentation, small barium sulfate particles, pollute the environment, etc., and improve the clarity. , The effect of less input equipment and lower barium ion content
- Summary
- Abstract
- Description
- Claims
- Application Information
AI Technical Summary
Problems solved by technology
Method used
Image
Examples
Embodiment 1
[0018] The production technology of by-product barium sulfate in the barium removal process of embodiment 1 yellow water may further comprise the steps:
[0019] (1) Obtaining yellow water: calcining celestite and reduced coal in a rotary kiln at a temperature of 1000-1250°C to obtain black ash, which is soaked in water to obtain an aqueous solution of strontium sulfide, that is, yellow water; Under the temperature of 80 DEG C, clear yellow water containing 8 g / l of barium ions was obtained after natural sedimentation for 6 hours to remove impurities of acid insolubles and calcium ions.
[0020] (2) Barium removal reaction: take 2m of clear yellow water 3 , and then spray and add 50 l of industrial dilute sulfuric acid with a mass concentration of 10% to carry out the barium removal reaction; continuously stir for 2 hours under the condition of 700r / min at a rotating speed to convert the barium ions into barium sulfate.
[0021] Wherein the equivalent ratio of barium ion to s...
Embodiment 2
[0025] The production technology of by-product barium sulfate in the barium removal process of embodiment 2 yellow water may further comprise the steps:
[0026] (1) Obtaining yellow water: calcining celestite and reduced coal in a rotary kiln at a temperature of 1000-1250°C to obtain black ash, which is soaked in water to obtain an aqueous solution of strontium sulfide, that is, yellow water; The clarified yellow water containing barium ions of 1.4 g / l was obtained after natural sedimentation for 5 hours at a temperature of 85° C. to remove impurities of acid insolubles and calcium ions.
[0027] (2) Barium removal reaction: take 2.4m of clear yellow water 3 , and then spraying and adding 90 l of industrial dilute sulfuric acid with a mass concentration of 2% to carry out the barium removal reaction; continuously stirring for 3 hours at a speed of 400 r / min to convert the barium ions into barium sulfate.
[0028] Wherein the equivalent ratio of barium ion to sulfate radical ...
Embodiment 3
[0032] The production technology of by-product barium sulfate in the barium removal process of embodiment 3 yellow water may further comprise the steps:
[0033] (1) Obtaining yellow water: calcining celestite and reduced coal in a rotary kiln at a temperature of 1000-1250°C to obtain black ash, which is soaked in water to obtain an aqueous solution of strontium sulfide, that is, yellow water; Obtain clear yellow water containing barium ions of 5 g / l after natural sedimentation for 4 hours at a temperature of 80° C. to remove acid-insoluble matter and calcium ion impurities.
[0034] (2) Barium removal reaction: take 2.8m of clear yellow water 3 , then spray and add 400l of industrial dilute sulfuric acid with a mass concentration of 1% to carry out the barium removal reaction; continuously stir for 5 hours under the condition of a rotating speed of 300r / min, so that the barium ions are converted into barium sulfate.
[0035] Wherein the equivalent ratio of barium ion to sulf...
PUM
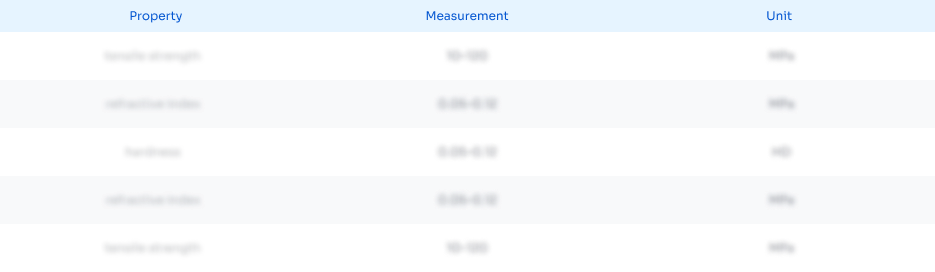
Abstract
Description
Claims
Application Information

- R&D Engineer
- R&D Manager
- IP Professional
- Industry Leading Data Capabilities
- Powerful AI technology
- Patent DNA Extraction
Browse by: Latest US Patents, China's latest patents, Technical Efficacy Thesaurus, Application Domain, Technology Topic, Popular Technical Reports.
© 2024 PatSnap. All rights reserved.Legal|Privacy policy|Modern Slavery Act Transparency Statement|Sitemap|About US| Contact US: help@patsnap.com