Device and process for separating silicon carbide waste mortar
A waste mortar and silicon carbide technology, applied in silicon carbide, carbide and other directions, can solve the problems of restricting process development, large water consumption, heavy pollution, etc., and achieve the effect of improving economic benefits, low water consumption, and large processing capacity
- Summary
- Abstract
- Description
- Claims
- Application Information
AI Technical Summary
Problems solved by technology
Method used
Image
Examples
Embodiment Construction
[0011] The present invention will be further described below in conjunction with accompanying drawing:
[0012] A device for separating silicon carbide waste mortar is provided with a cyclone separator, a feed pipe, an underflow main pipe, an overflow main pipe, a feeding box and a feeding pump, and the structure of the cyclone separator is as follows: figure 1 As shown, there is a housing 2, a feed pipe 3 is provided on the involute direction on one side of the housing 2, an overflow pipe 1 is provided above, a straight column section 4 is provided below the housing 2, and a straight column section 4 A conical cylinder 5 is provided below, and a bottom flow port 6 is provided below the conical cylinder 5. The structure and connection method of the above-mentioned components are the same as those of the prior art, and will not be described here. When the cyclone separator is working, the silicon carbide Under the pressure of about 0.3MPa, the slurry enters the shell 2 from the...
PUM
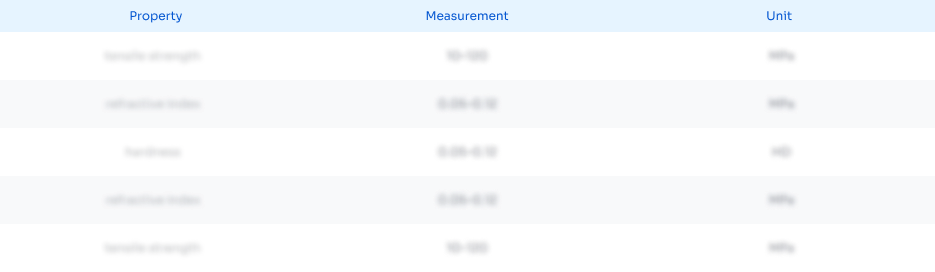
Abstract
Description
Claims
Application Information

- R&D
- Intellectual Property
- Life Sciences
- Materials
- Tech Scout
- Unparalleled Data Quality
- Higher Quality Content
- 60% Fewer Hallucinations
Browse by: Latest US Patents, China's latest patents, Technical Efficacy Thesaurus, Application Domain, Technology Topic, Popular Technical Reports.
© 2025 PatSnap. All rights reserved.Legal|Privacy policy|Modern Slavery Act Transparency Statement|Sitemap|About US| Contact US: help@patsnap.com